In construction, a successful project often begins before the first brick is laid or the first steel beam is erected.
It often starts with a collaborative preconstruction process that serves as the inflection point where design becomes even more grounded in reality. A process where the owner, design team, and contractor work closely together and hold each other accountable. Here, design details begin to take shape, and alternate options are taken into consideration. Timely and accurate feedback on cost, schedule, and constructability is critical.
Our Preconstruction Team, led by Patrick Descant, Vice President of Preconstruction, thrives in these situations. The goal for his team is simple: through team buy-in, foster collective responsibility and develop the most efficient design possible using the best materials available within an accurate budget.
The process: overcoming challenges through teamwork.
“On paper, the process can seem simple enough,” says Patrick. “But in reality, we’re often dealing with many different variables and constraints at this time in a project’s lifecycle from budget and schedule demands to market volatility and the availability of desired materials. It takes a great deal of trust, coordination, and industry knowledge with our trade and design partners to get a project shovel ready.”
This is because projects are often met with unforeseen challenges. However, through preconstruction, these challenges can be identified early and often mitigated with little or no impact on the overall project. Our recently completed project, The Wellness Center at Bayou Bend, is a great example.
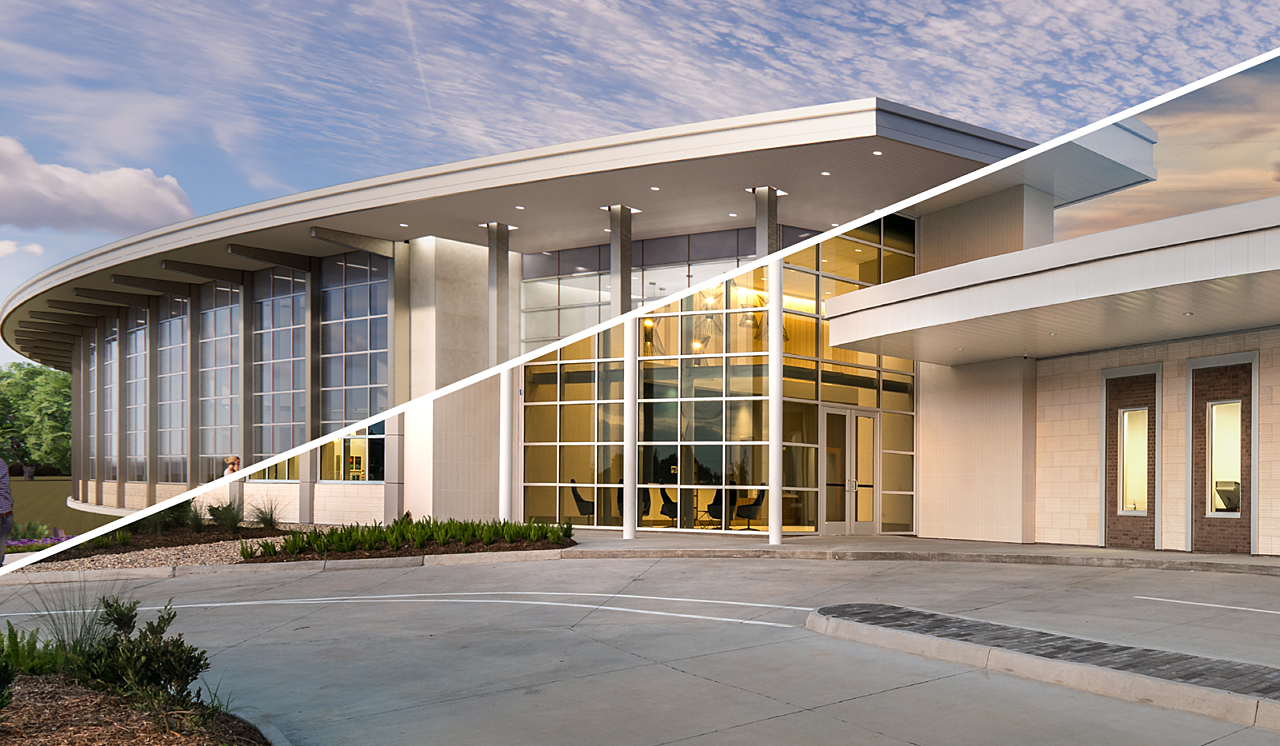
Preconstruction in practice: The Wellness Center at Bayou Bend.
After being awarded the project through a competitive interview process, our Preconstruction Team began immediately collaborating with the owner and design team during schematic design. At this time, the building’s square footage and floorplate had been established. As we began the first budgeting phase, we quickly realized, due to the onset of the global pandemic and related supply chain, labor, and market volatility, that the budget would be a challenge.
“Our focus was clear,” says Patrick. “As we moved further into design development, our team would need to identify as many cost-saving ideas as possible for the owner that could bring the budget in line without sacrificing quality or programming needs.”
In total, we would identify more than $4 million in options equal to 25% of the original construction budget.
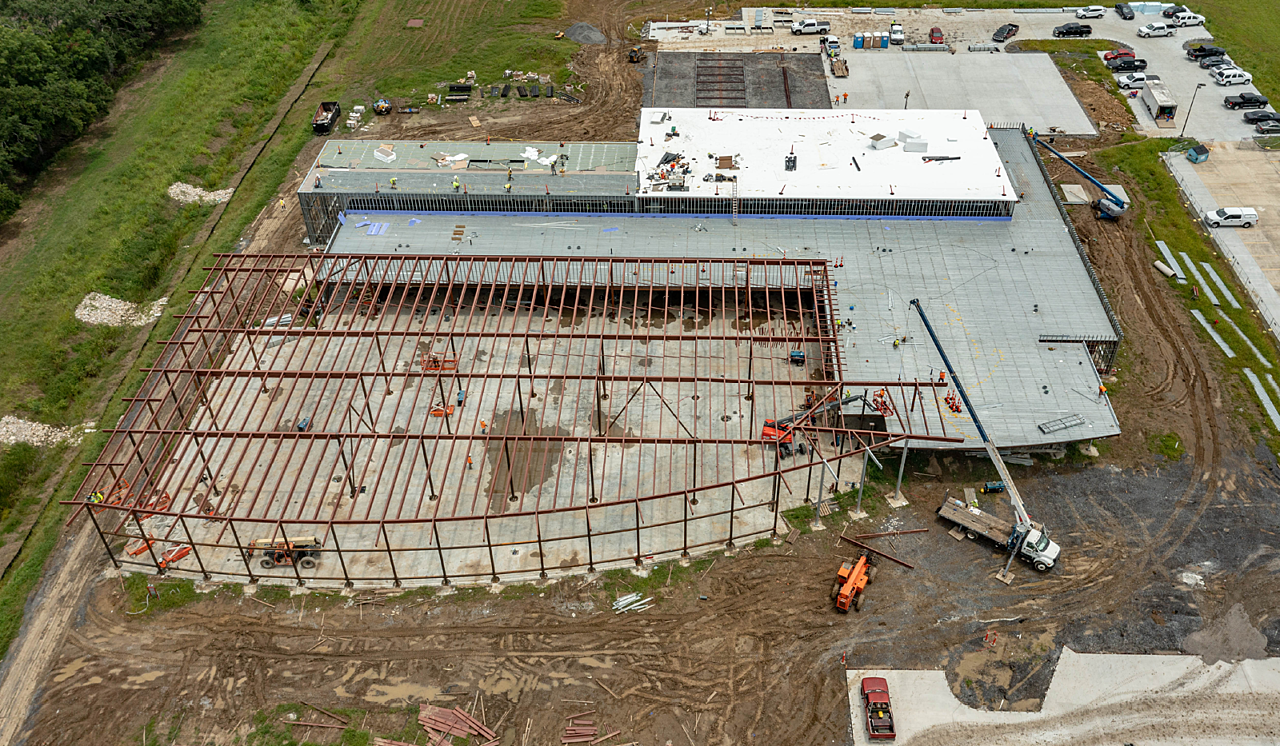
Understanding the potential impact to the project, and the high volatility of the steel market, we charged our structural engineer with changing the structural design to accommodate beams rather than bar joists.
This was critical for keeping the project moving forward on schedule.
As a result, our team was able to lock in our steel supplier as early as 60 percent design. Not only was this critical given the increasing cost of the material, but also due to the nationwide warehouse expansion projects that took the availability of bar joists out of the private market.
In the end, early commitment to our design and trade partners and project investment would prove wise. Many system changes were needed to bring the budget in line, and this trust and commitment would help steer the project in the right direction.
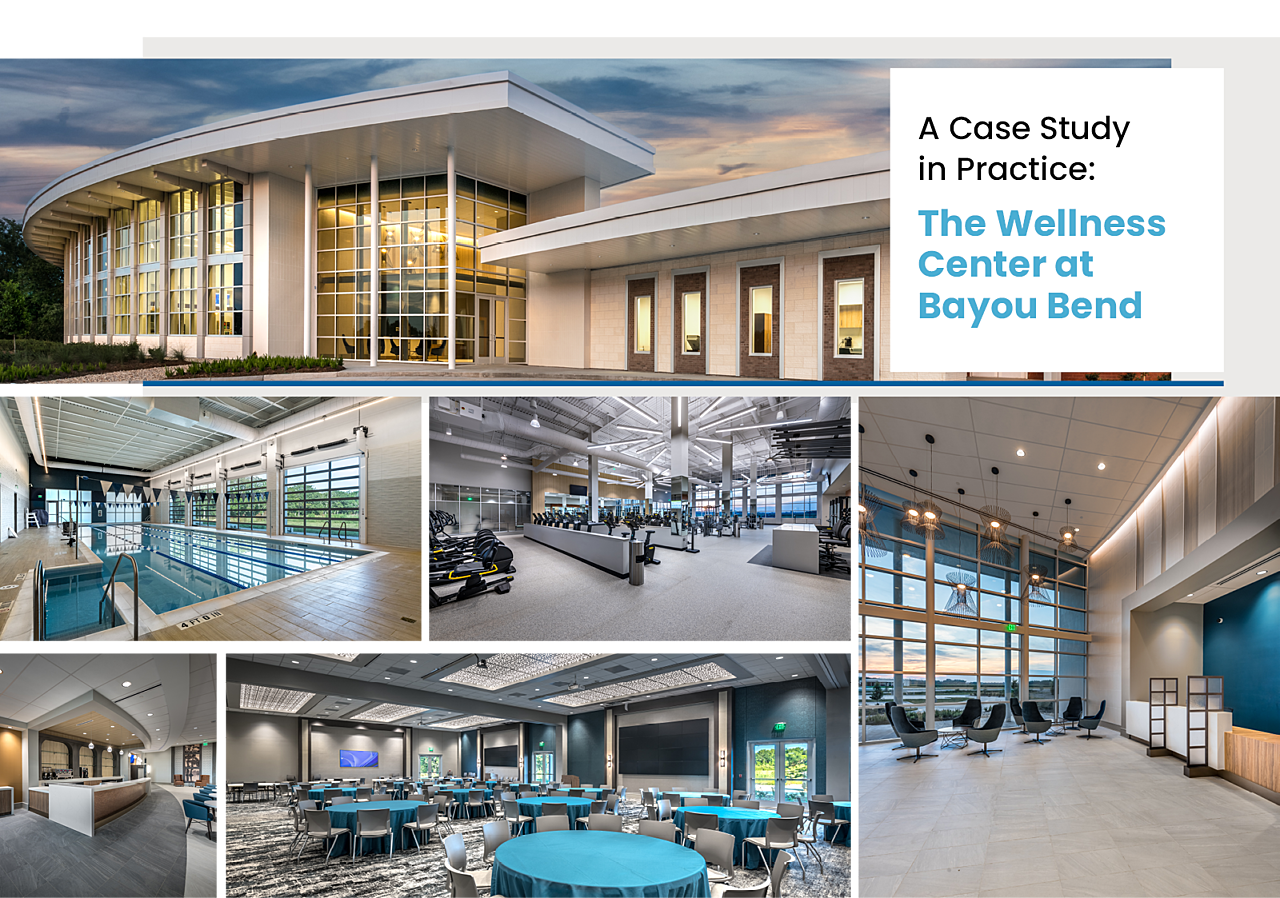
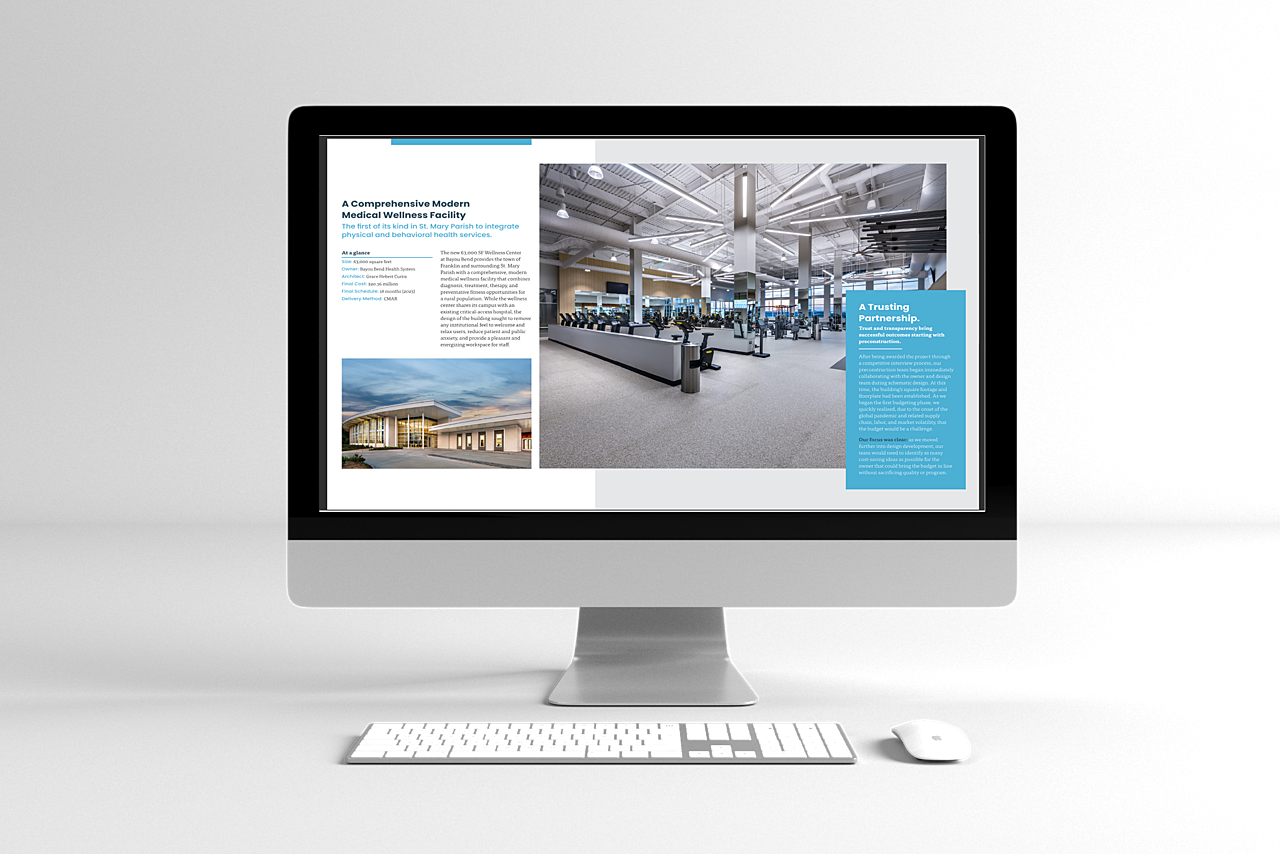
A Comprehensive Modern Medical Wellness Facility
The new 63,000 SF Wellness Center at Bayou Bend provides the town of Franklin and surrounding St. Mary Parish with a comprehensive, modern medical wellness facility that combines diagnosis, treatment, therapy, and preventative fitness opportunities for a rural population.
The design of the building removes any institutional feel to welcome and relax users, reduce patient and public anxiety, and provide a pleasant and energizing workspace for staff.
Trust is critical with this many moving parts.
In more than 40 years, we’ve earned our reputation as a trusted partner throughout the construction process, in part from a robust and critical preconstruction process. Most recently in the last decade, we’ve seen a trend towards more collaborative delivery methods where preconstruction is becoming more widely used.
In just the last five years, more than 75% of our projects have included preconstruction with several active projects currently in the preconstruction phase.
“This experience has given us ample opportunity to refine our process,” says Patrick. “We’re always looking for ways to reduce project risk, better control costs, and include our trade partners as early as possible. Close collaboration with the design team is critical. In the end, it’s better for the client and the project as a whole.”
For more information on our preconstruction process and related projects, please visit our website.
Noteworthy Projects & Recent Completions
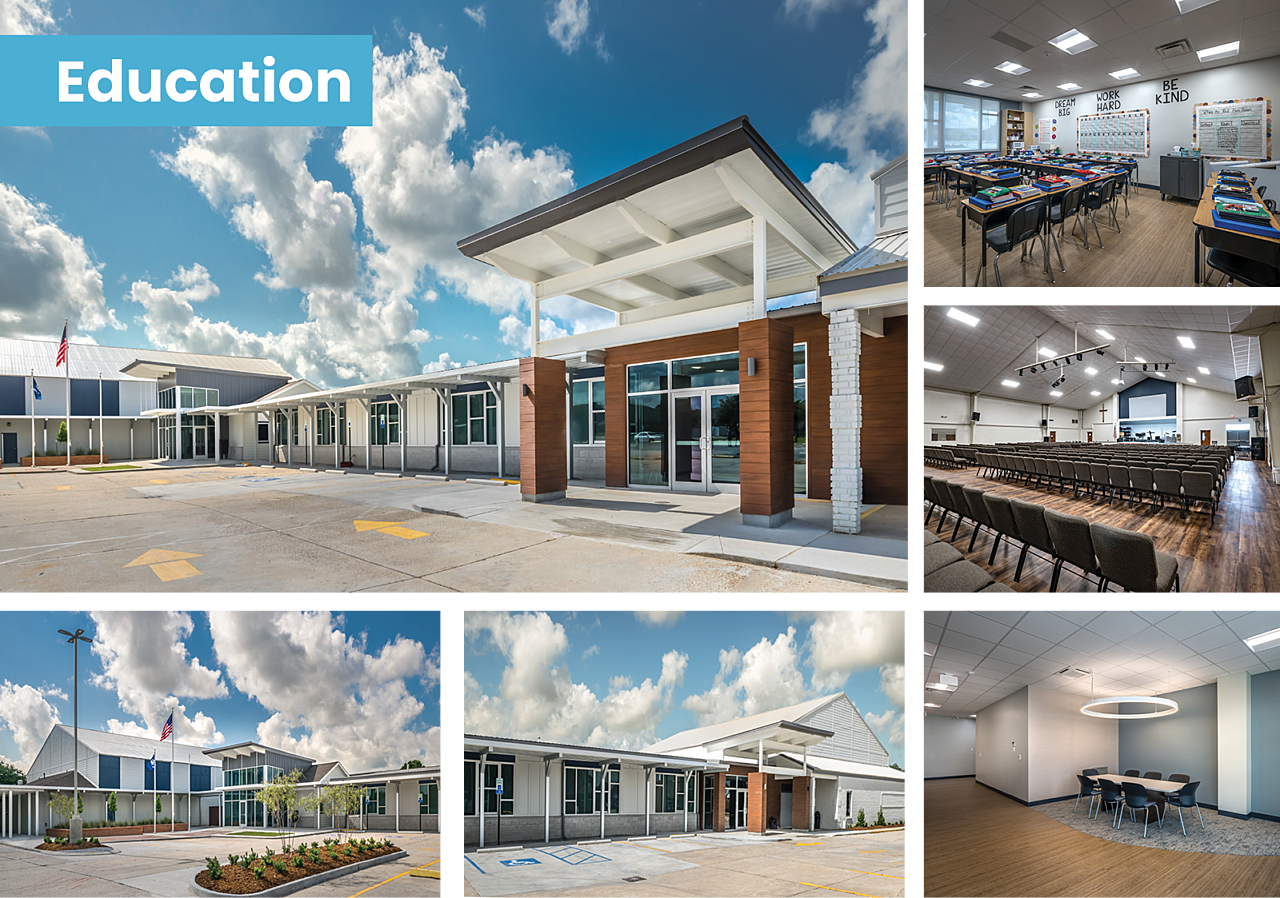
Houma Christian School
Houma Christian School has a fresh, updated campus. This renovation spanned two phases: Phase 1 addressed repairs from previous storm damage and included interior renovations for the elementary hall. Phase 2 saw additional renovations for the remaining campus.
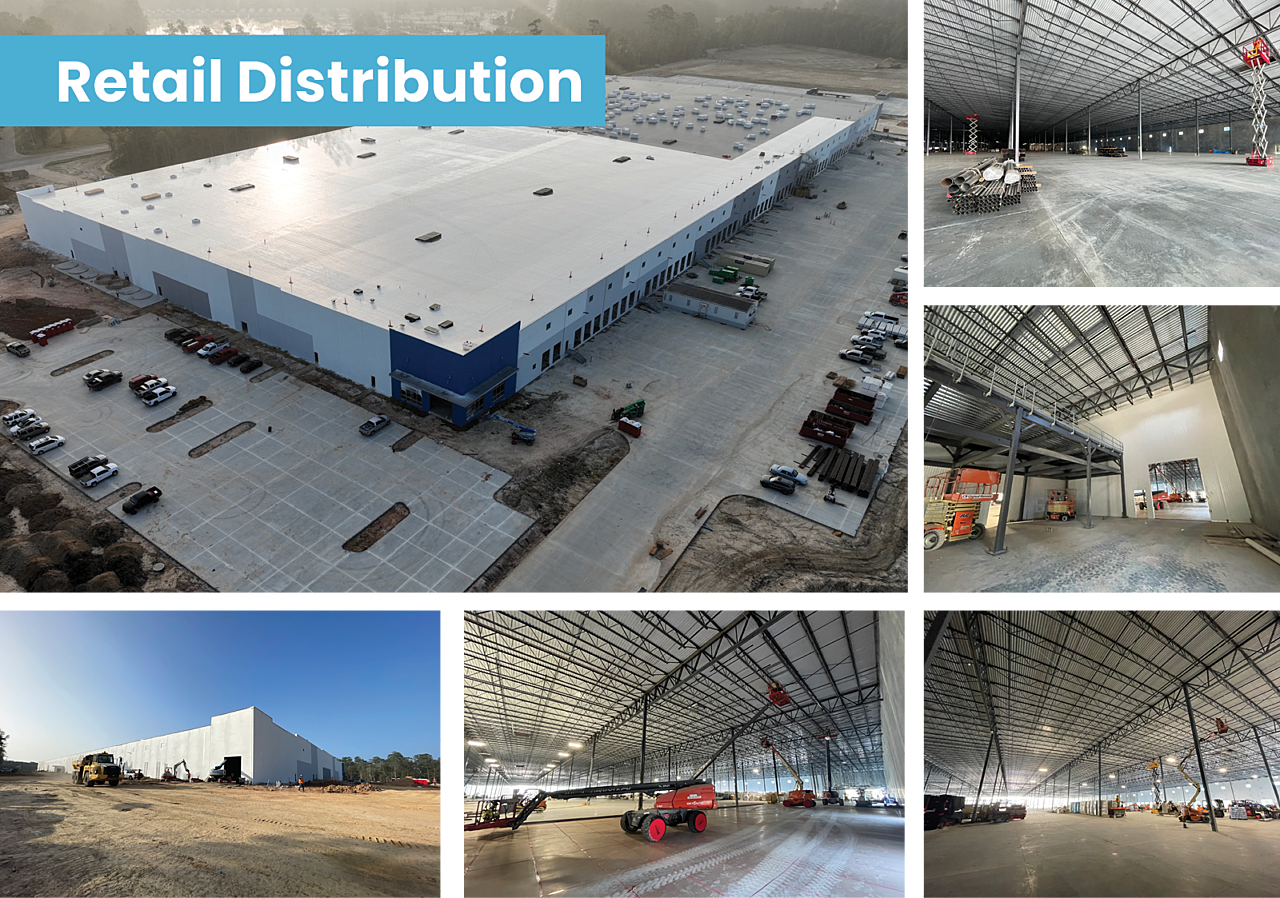
Niagara Bottling
In partnership with nationwide contractor Choate Construction Company, our team is hard at work on an extraordinary project – a new 500,000 SF facility for Niagara Bottling, one of the nation's leading beverage manufacturers. This new facility will contain advanced equipment and technology that will increase production efficiency to allow the company to meet growing demand.
Resource Bank
We continue to make great progress on the new 18,000 SF branch office for Resource Bank. When complete, it will include banking and office space on the first floor, shell spaces for future office build-outs on the second and third floors, and private conference/event space with a rooftop terrace on the fourth floor.
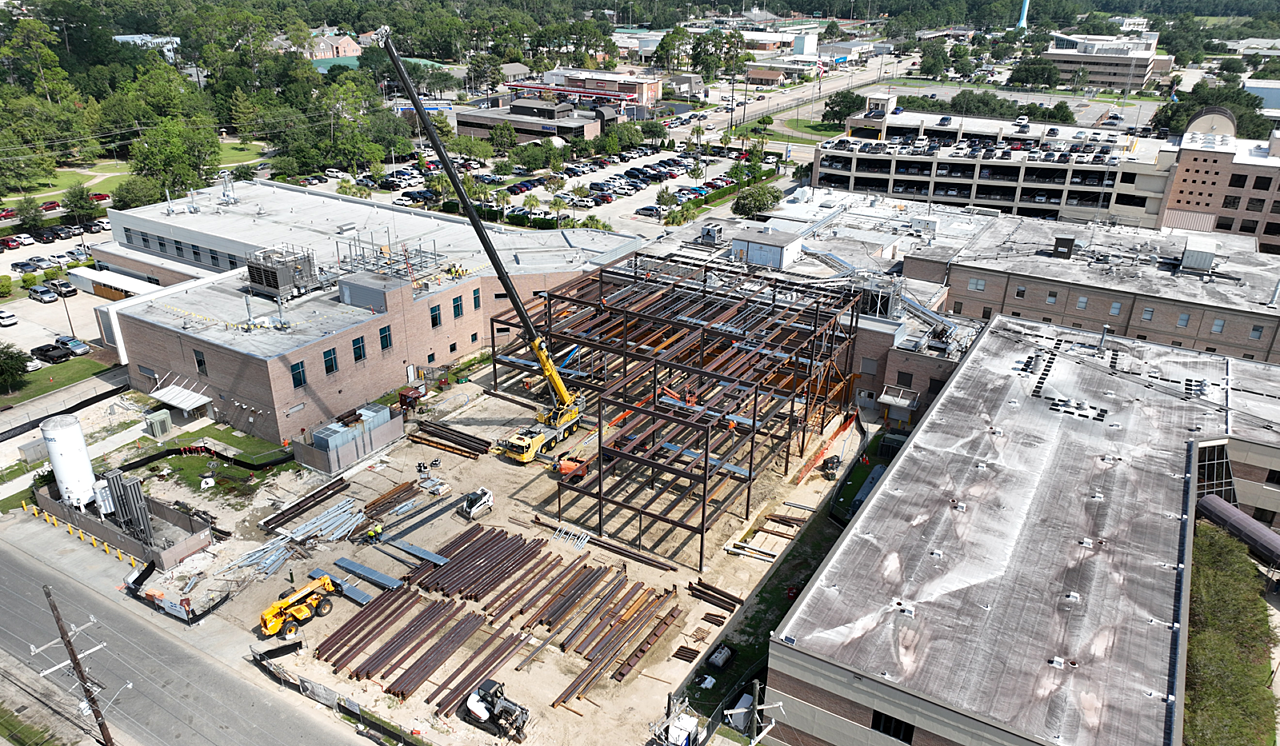
Slidell Memorial Hospital
The new 60,000 SF, $34 million addition to Slidell Memorial Hospital will expand the hospital's main campus with a brand-new set of operating suites, an additional ICU, and an additional inpatient care unit. The project is set for completion in early 2025.
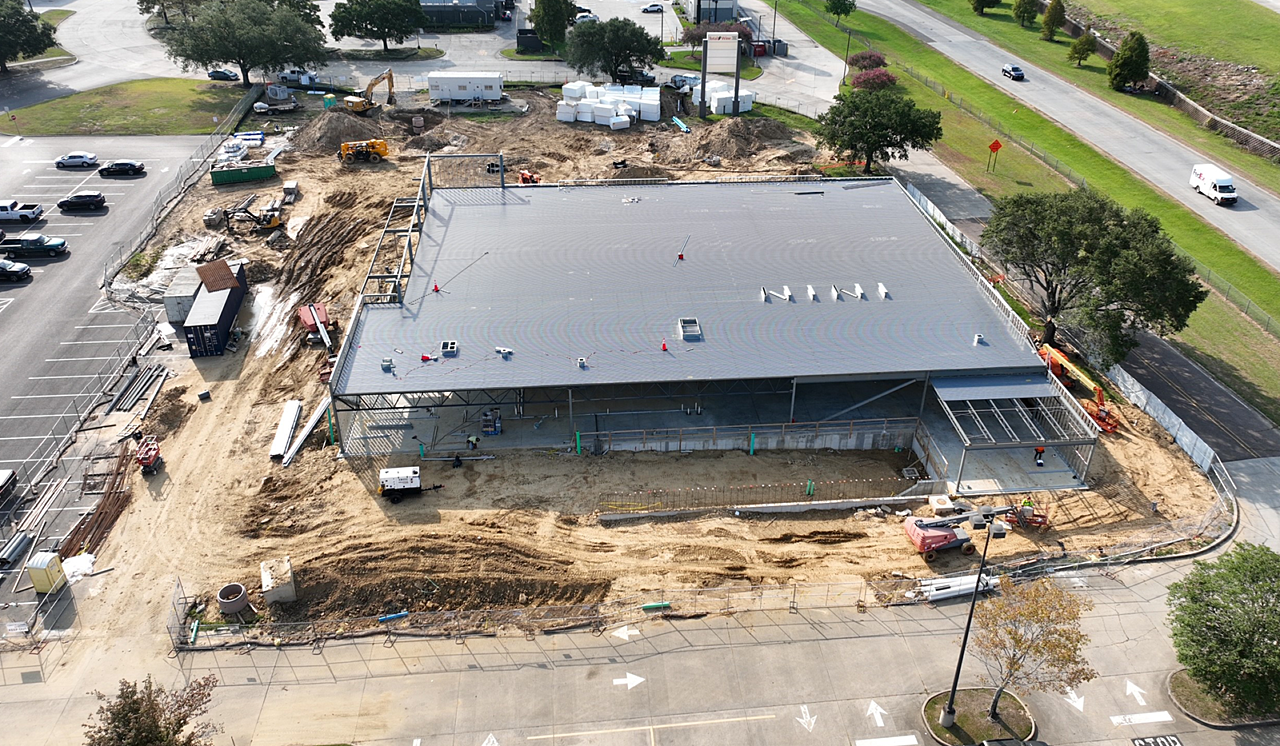
Aldi 83 and 71
DonahueFavret is currently building two new Aldi stores in the Baton Rouge area - one on Siegen Lane (pictured) and one on O'Neal Lane. Similar to Aldi Slidell, these ground-up retail facilities are just over 20,000 SF, and are on track for completion later this year.
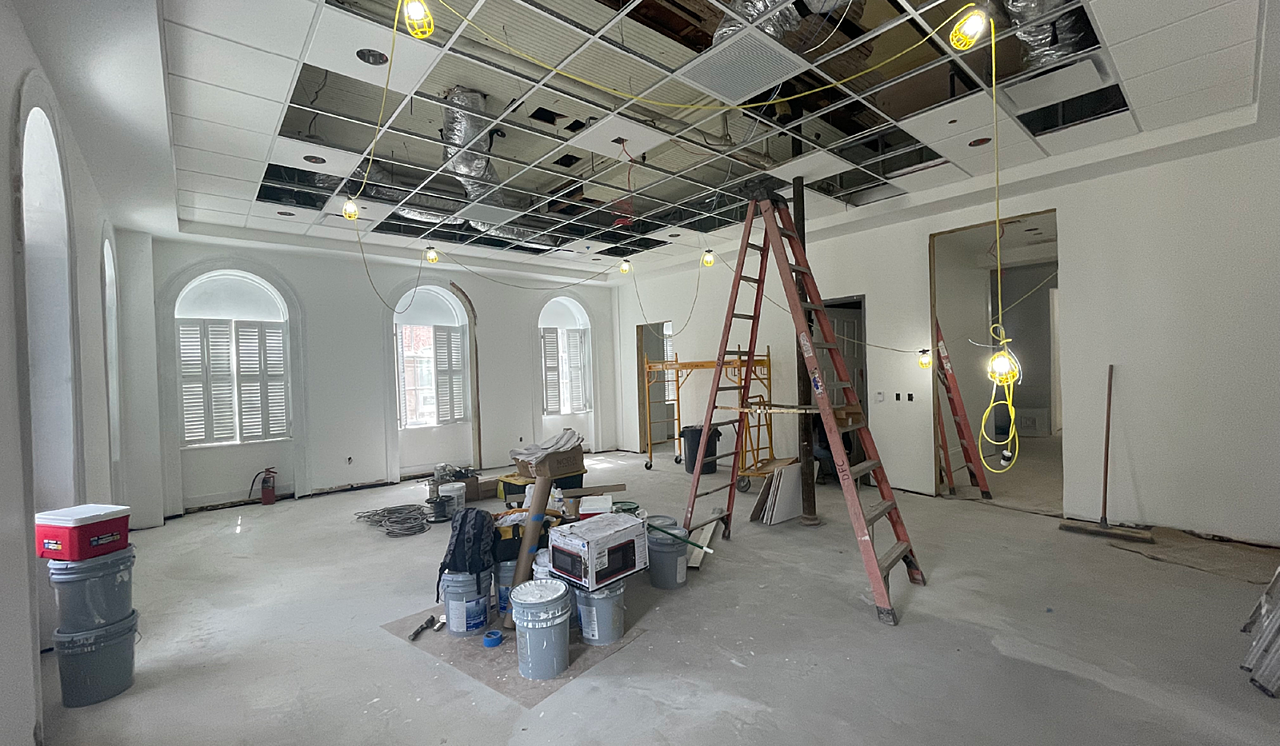
Poydras Home Renovation
After recently completing the 60,000 SF new addition to Poydras Home in uptown New Orleans, our team is currently renovating the existing historic facility, representing phase two of the project.
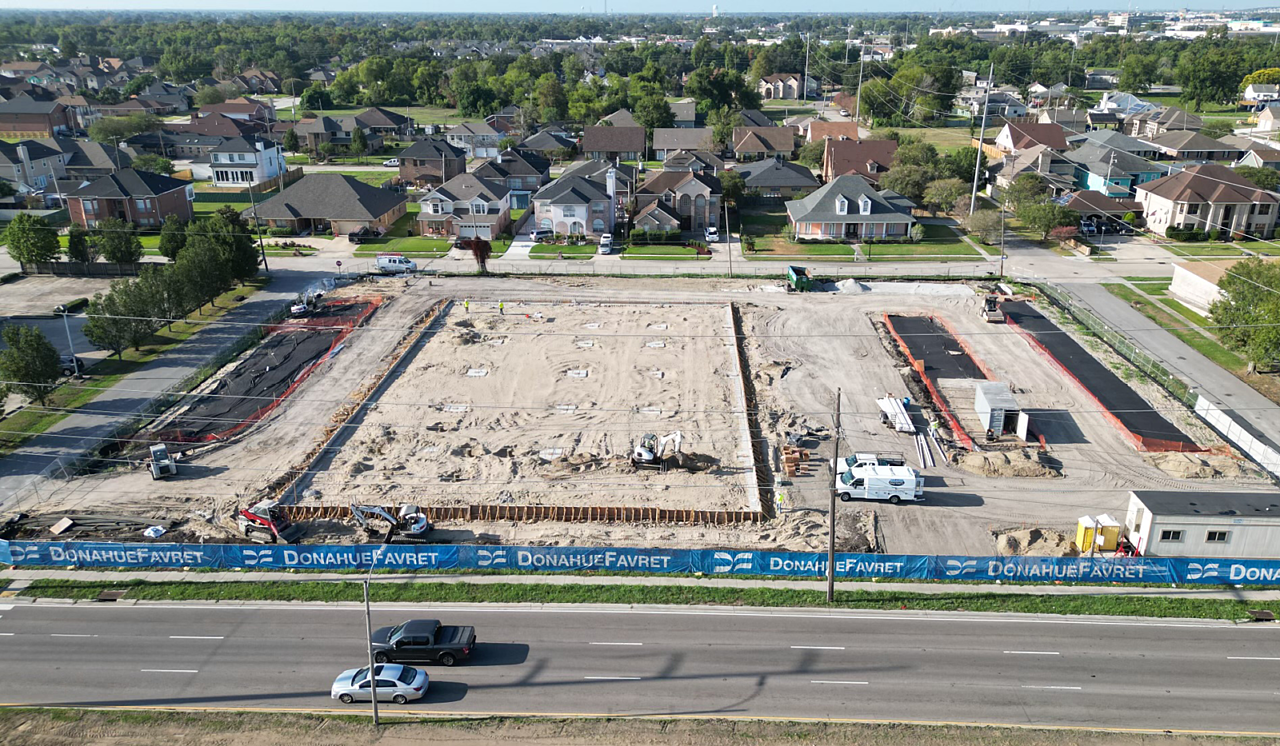
Ascension Algiers
This 20,000 SF ground-up medical facility will bring much needed extended health services to the Algiers community. With more than 180 timber piles going in, we’re off to a great start for completion next fall.
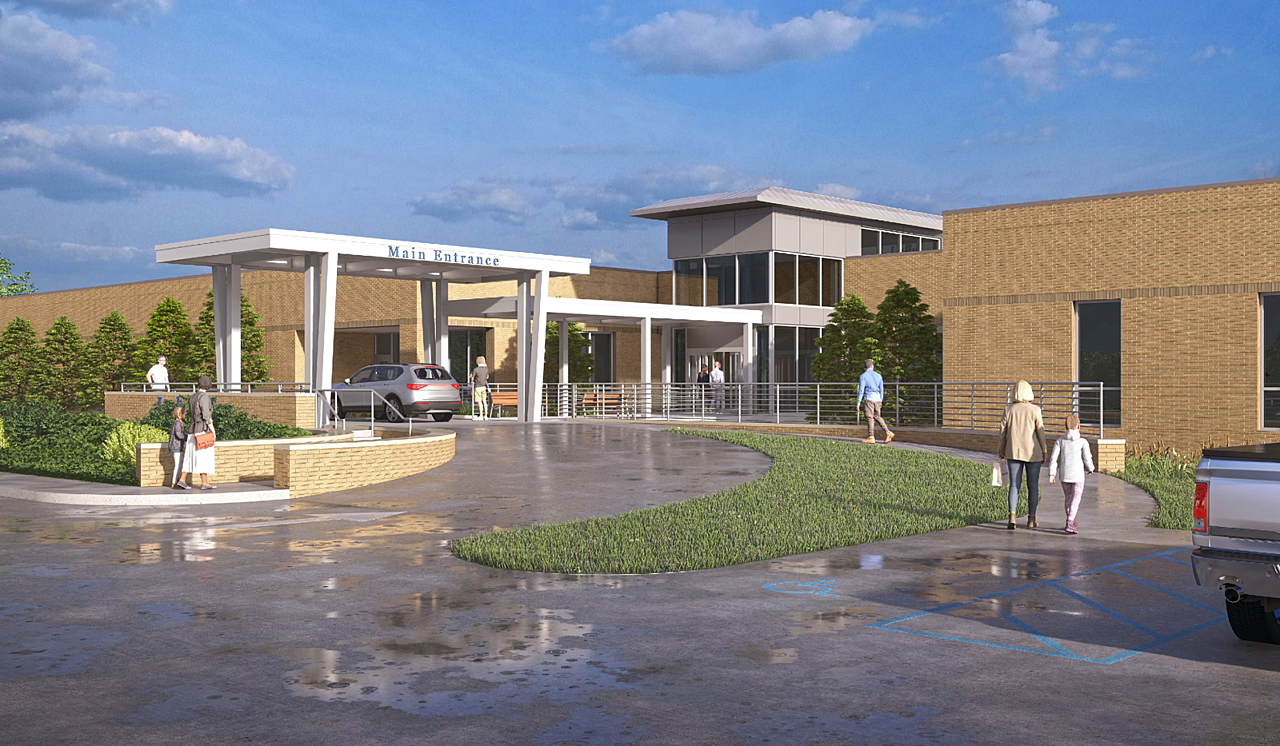
Lady of the Sea
DonahueFavret was recently awarded this CMAR project with Lady of the Sea General Hospital. After being severely damaged during Hurricane Ida, the new ground-up 80,000 SF hospital will include 23 inpatient med surg beds, ICU Unit, emergency, radiology, labs, and cardiopulmonary services, among others.
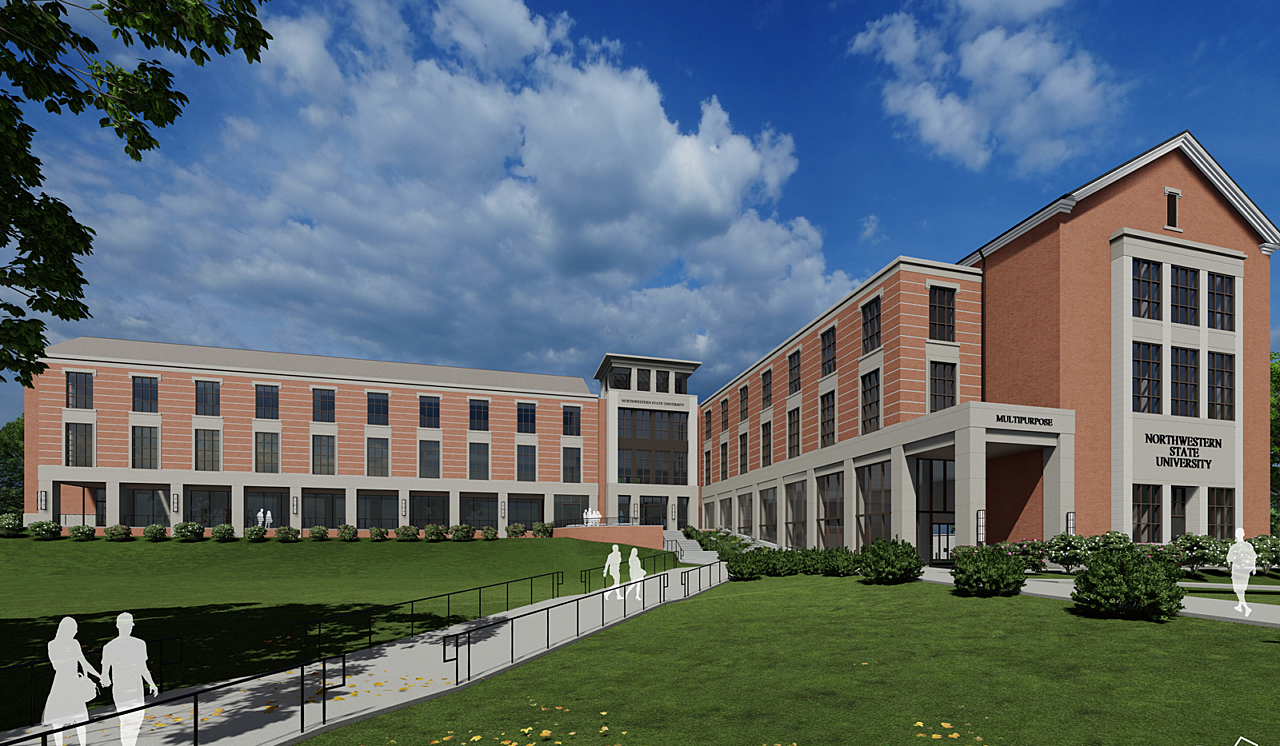
Northwestern State University Alost (Kyser) Hall
We have just begun construction on the new 72,000 SF multi-story classroom and administrative building at Northwestern State University after recently completing the preconstruction process with the owner and design team. The building will consist of multi-purpose classrooms, teaching labs, simulation clinics, administrative offices, student collaboration spaces, and support areas.
Driving FORE Charity back for another round
It's almost tee time!
We can't wait to see everyone in just a few weeks for our third annual Driving FORE Charity golf tournament. We are sold out of team spots! For anyone still interested in sponsoring the event, please contact Lauren Andrews at 985.626.4431 or at laurena@donahuefavret.com as soon as possible. Time is running out!
