Following a two-year slowdown, construction of light industrial facilities is showing signs of recovery.
A renewed growth in e-commerce and shifting trends in supply chain management may be signaling increased demand for light industrial facilities such as warehouses and distribution centers now and into next year. In a study from Interact Analysis, the impacts of COVID-19, as in many market sectors, brought a slowdown in demand for real estate over the last two years, stemming from higher interest rates and the reduction of available capital.
This forecasted change in demand, however, is multi-faceted. For one, analysts suggest that e-commerce growth rates are rapidly increasing – some even suggest a return to double-digit growth. Couple this with what some are calling a shift from “just-in-time” to “just-in-case” supply chain management, and we start to see a more positive outlook for the demand of these types of facilities.
As e-commerce returns to pre-pandemic levels, and companies require higher inventory on-hand, the demand for more capacity becomes apparent.
What does this mean for construction?
Aside from the proposed increase in demand (and therefore more potential new project opportunities), there’s a renewed interest in understanding how design and construction of these facilities is changing – and what trends are shaping decisions and impacting the building process.
Larger Building Footprint
Because of the shift away from “just-in-time” delivery, we’re seeing a trend toward larger facilities with greater available space to hold more inventory. Larger facilities mean greater levels of coordination needed between design and trade partners, often working with a variety of subcontractors. Greater attention to planning, critical path items, and phasing of these large-scale facilities is critical.
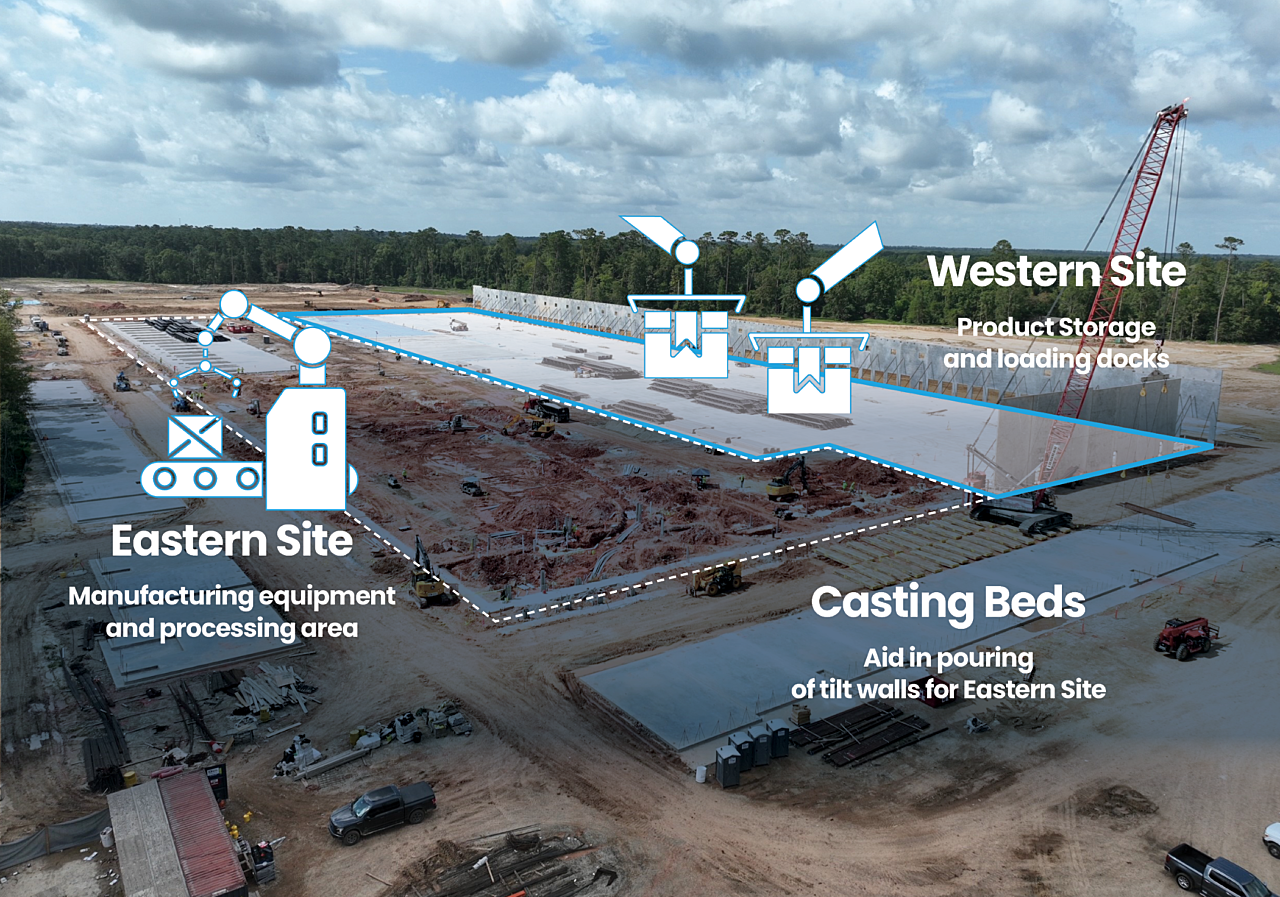
Construction of the Niagara Bottling Facility was separated into two distinct areas built simultaneously: product storage and loading docks are situated along the western half of the facility, while Niagara’s core manufacturing equipment and processing area are in the eastern half. This proprietary equipment required careful planning and consideration throughout construction.
Efficient Construction Methods
Most industrial facilities, from heavy and light manufacturing to distribution centers, focus primarily on functionality and “no-frills” design aesthetics. Speed to market is critical. To achieve this, many owners will gravitate toward a design-assist delivery method supported by prefabrication. By doing so, portions of the building can be built offsite and assembled onsite, allowing for a faster construction process and minimal disruption to other trades working in the same area.
Efficiency, especially in the construction of these types of facilities, also comes in the use of tilt walls. These exterior facade concrete walls are cast-in-place onsite and then tilted into place. They serve as the structure and skin of the building and provide insulation properties. This method allows multiple portions of the building and site to progress simultaneously without disrupting the schedule.
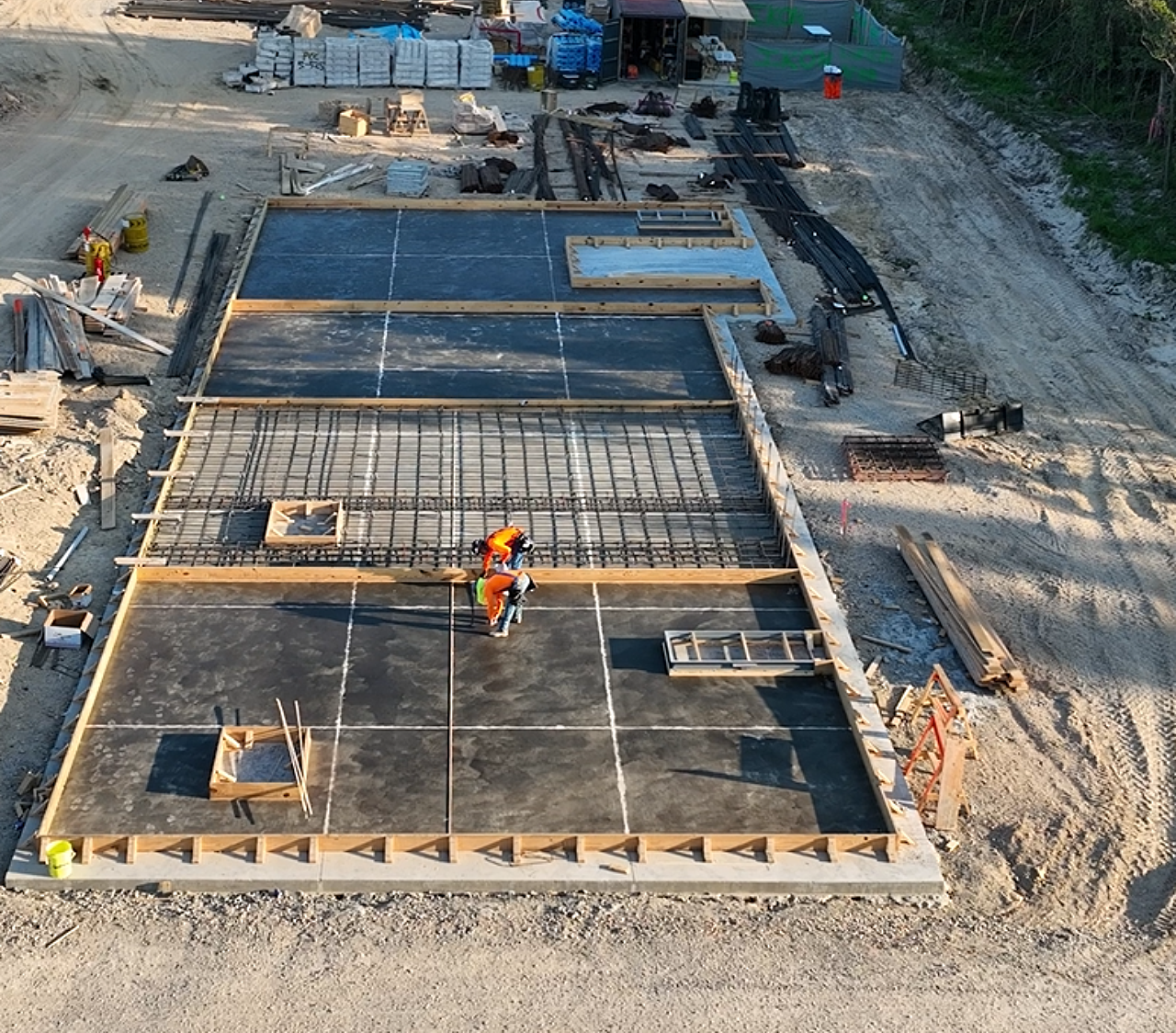
Construction of the Niagara Bottling Facility was separated into two distinct areas built simultaneously: product storage and loading docks are situated along the western half of the facility, while Niagara’s core manufacturing equipment and processing area are in the eastern half. This proprietary equipment required careful planning and consideration throughout construction.
Design for Growth
With higher on-hand inventory, the need to optimize for maximum space use is important, especially in regions where land is costly and limited. We see the need to build taller facilities to leverage vertical storage. This in turn requires more focus on the live loads of stored materials and the weight of specialty equipment. Additional bracing and thickened slabs may be necessary. Additionally, facilities will look to future growth through horizontal expansion. In Niagara's case, the building had one of four sides constructed out of steel framing that could be easily removed and expanded when additional square footage was required.
Looking Forward
As technology improves, new facilities will require more built-in flexibility in place to further integrate advances in tools and equipment. We’re already seeing the introduction of smart technologies like automated picking tools, automatic guided vehicles (AGVs), and the internet of things (IoT).
Construction of light industrial facilities does present several challenges, but the advantage is found in their diversity, forcing designers and contractors to continually adapt to unique requirements of each business type and the space they need.
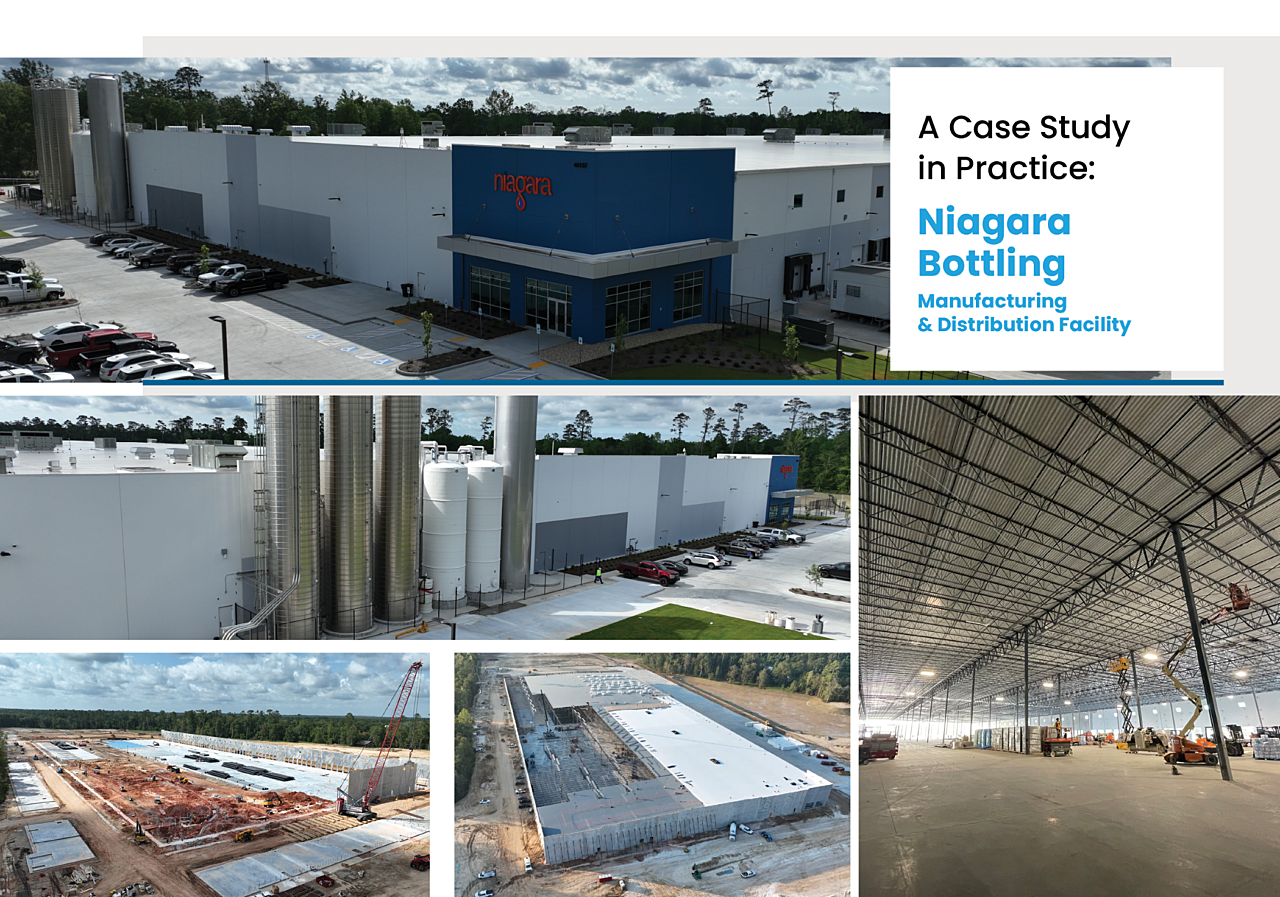
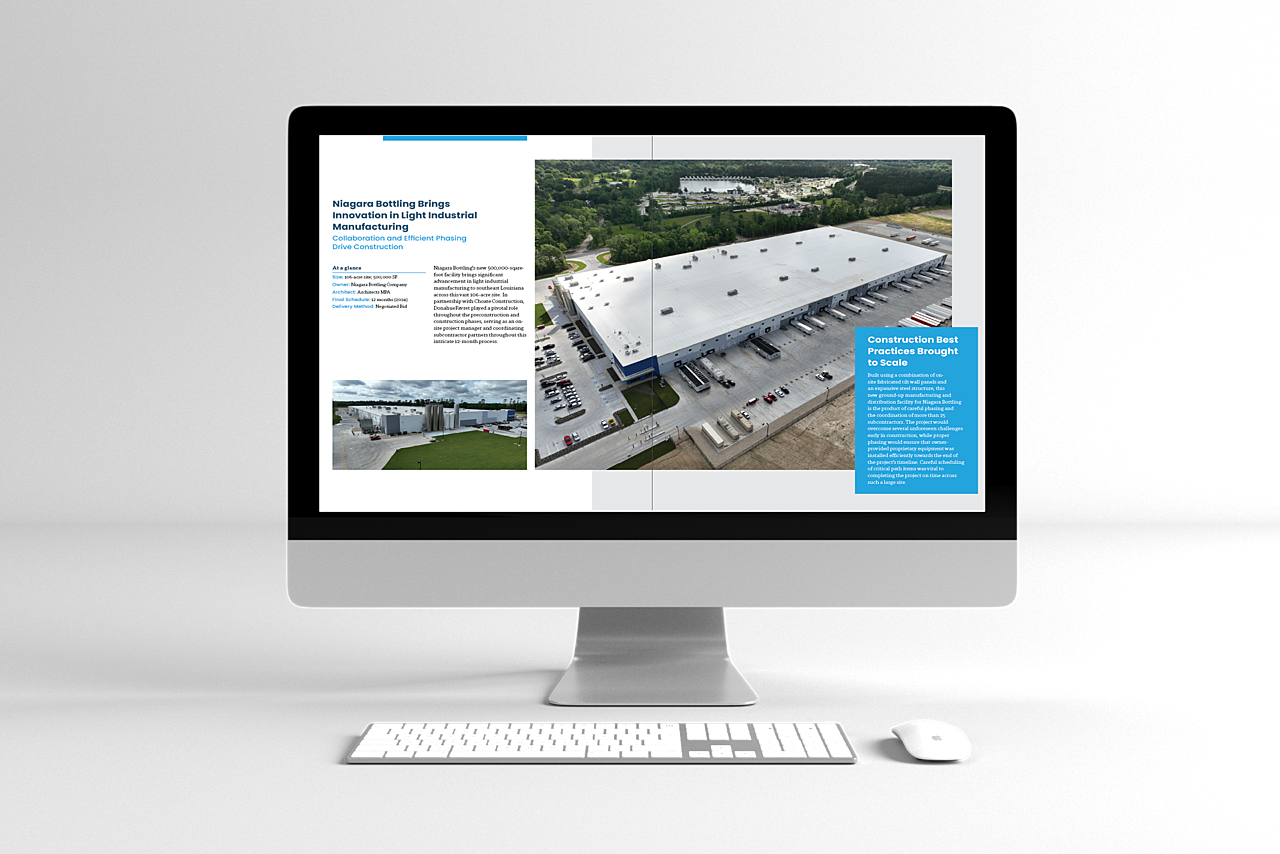
Niagara Bottling Brings Innovation in Light Industrial Manufacturing
Niagara Bottling’s new 500,000-sqare-foot facility brings significant advancement in light industrial manufacturing to southeast Louisiana across this vast 106-acre site.
In partnership with Choate Construction, DonahueFavret played a pivotal role throughout the preconstruction and construction phases, serving as an on-site project manager and coordinating subcontractor partners throughout this intricate 12-month process.
Noteworthy Projects & Recent Completions
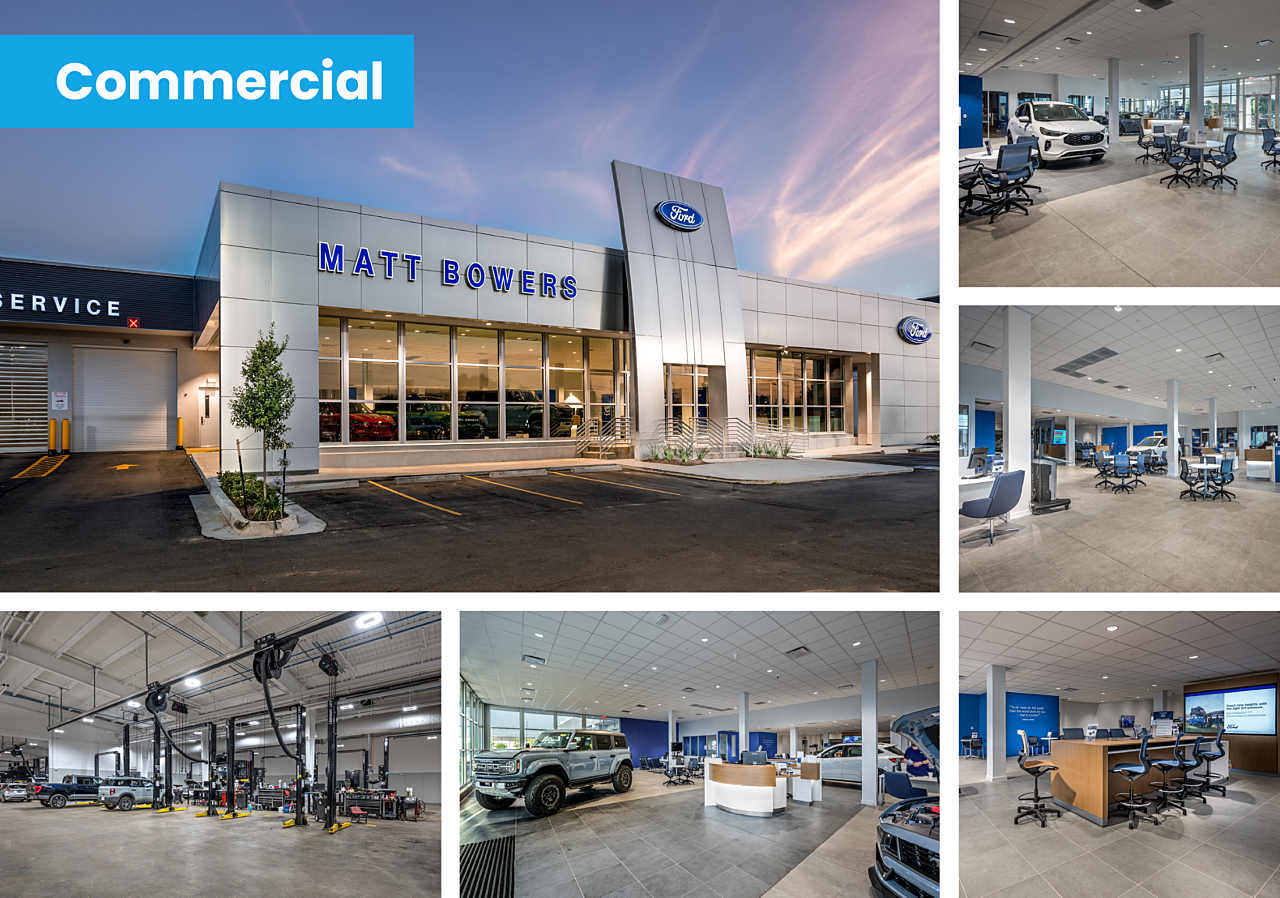
Matt Bowers Ford
The 40,228 SF Matt Bowers Ford auto dealership underwent a comprehensive remodel. Phases 1 and 2 focused on upgrading the automotive shop spaces, prioritizing enhancements in functionality and safety. The renovated automotive shop now includes more than 40 service bays. Phase 3 of the remodel focused on the showroom, completely revamping its facade to align with the brand's vision.
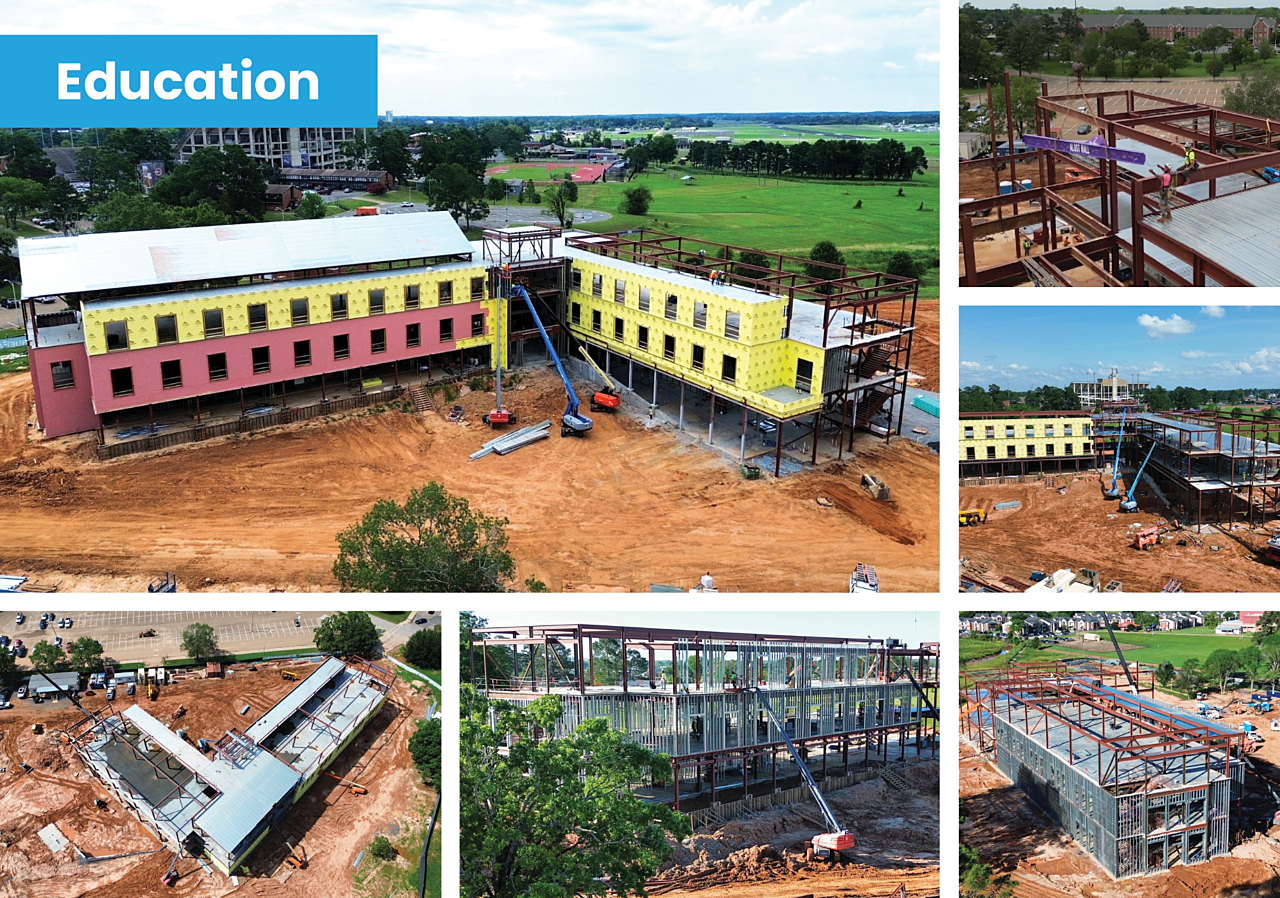
Northwestern State University Alost (Kyser) Hall
After a successful beam signing event in May, our team continues to make great progress on this new 72,000-square-foot multi-story classroom for Northwestern State University When complete, the building will consist of multi-purpose classrooms, teaching labs, simulation clinics, administrative offices, student collaboration spaces, and support areas.
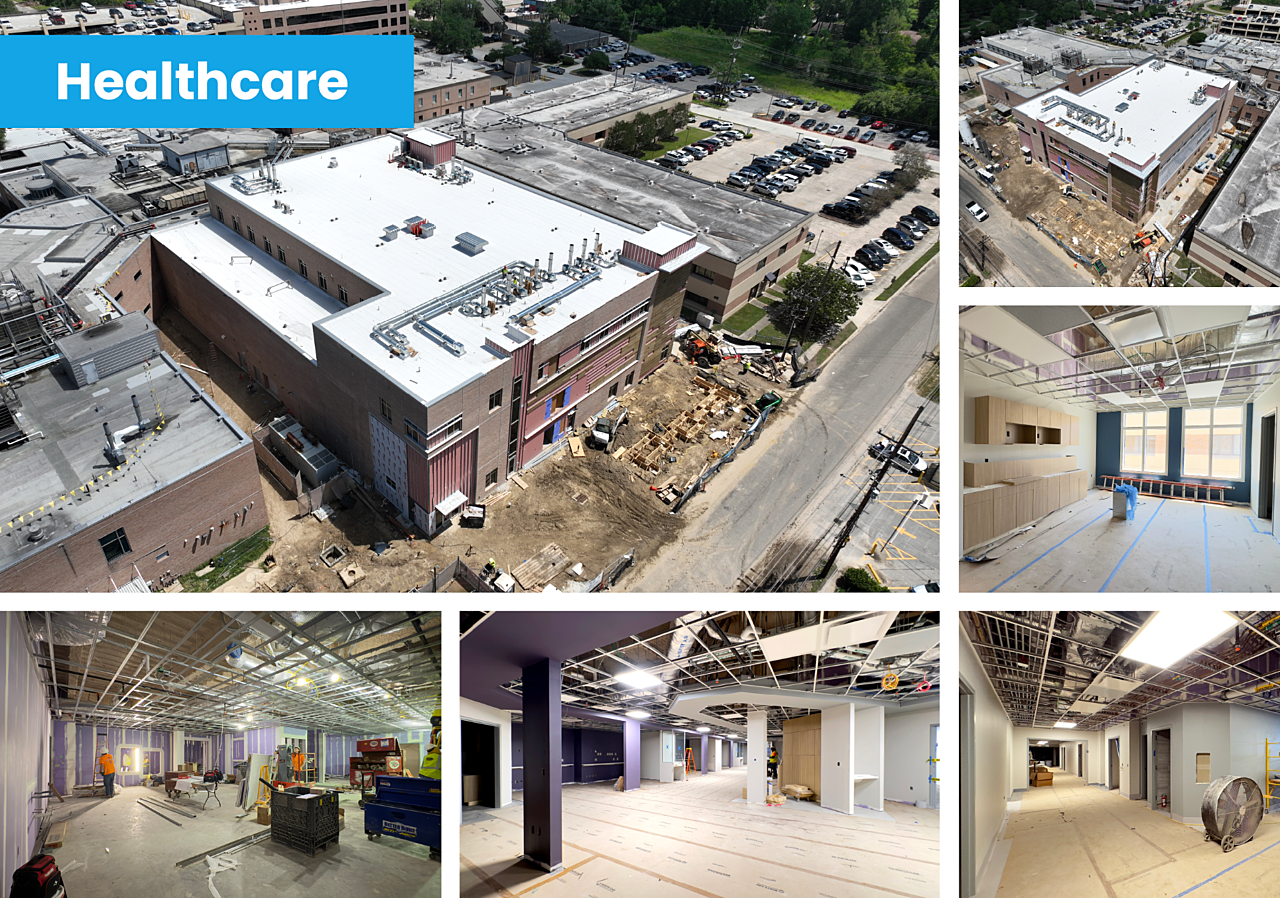
Slidell Memorial Hospital
Progress continues at Slidell Memorial Hospital's new three-story addition. The project will expand the main campus of the hospital and will house a brand-new set of operating suites, an additional Intensive Care Unit, and an additional inpatient care unit. The project also includes the demolition of existing structures and renovation of the current operating rooms.
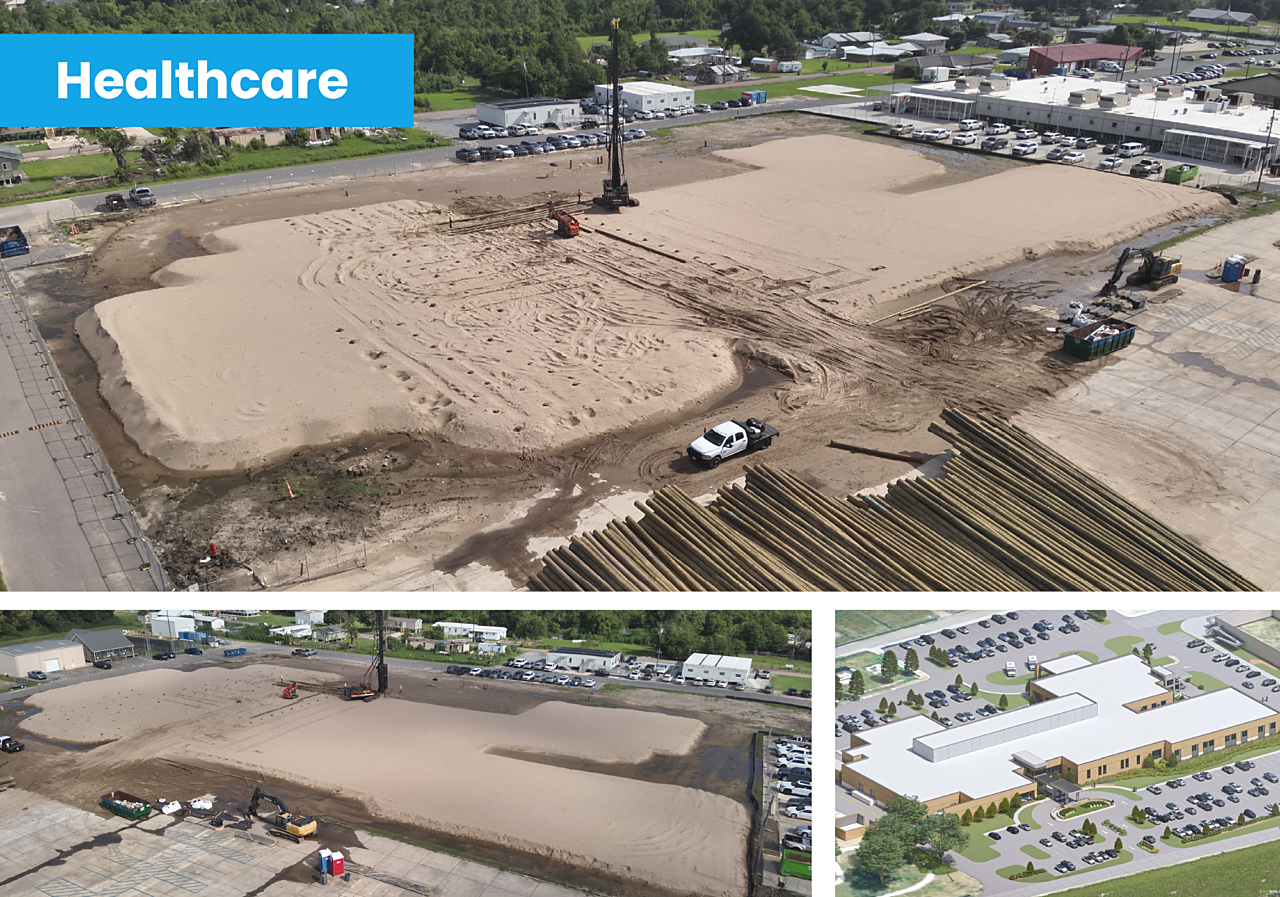
Lady of the Sea General Hospital
The new ground-up 80,000 SF hospital for Lady of the Sea is now underway with our team on site driving more than 1,700 70-foot timber piles. Following the pile-driving process, we will be working on the underground foundation for the next three months.
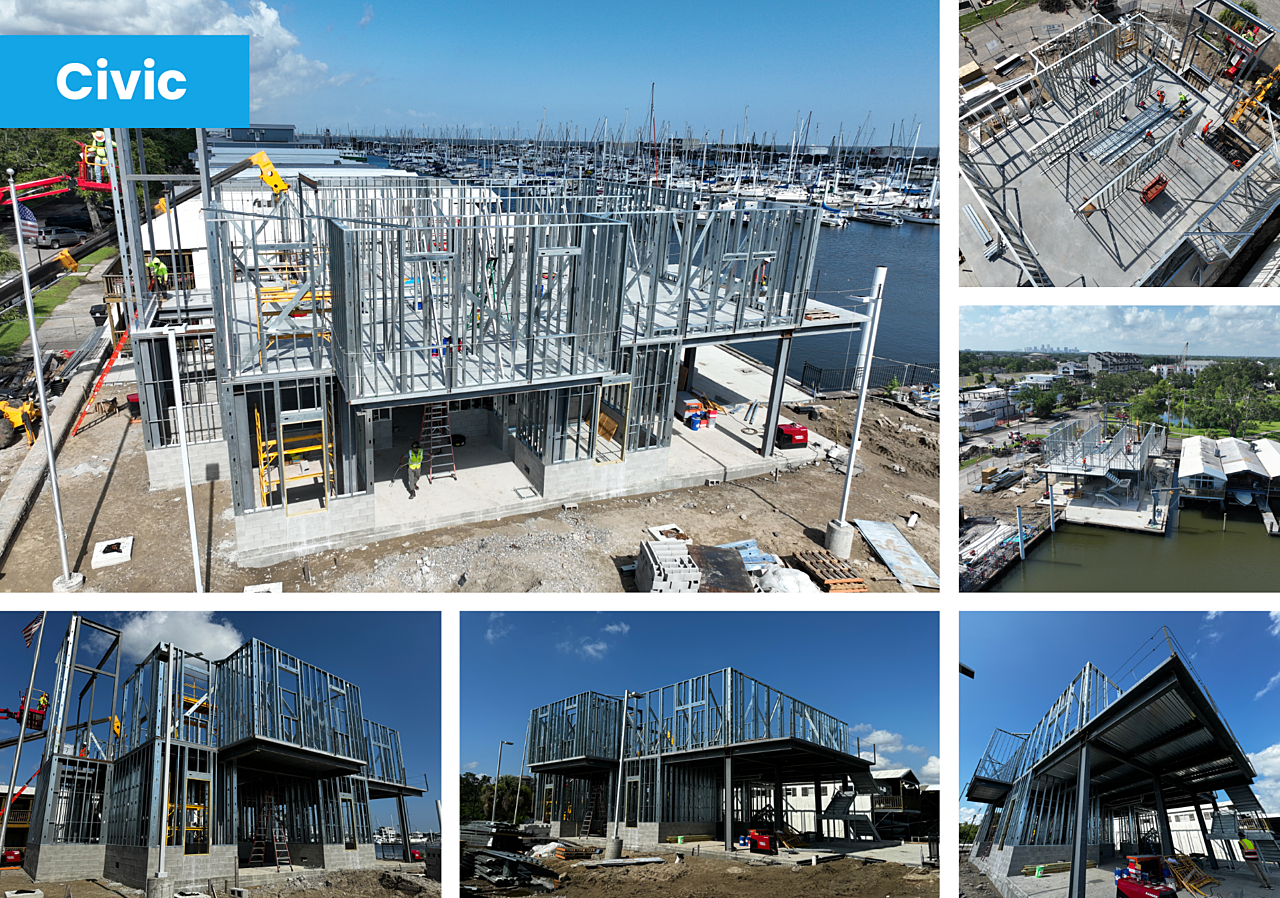
Community Sailing
Our team is making great progress on the new Community Sailing Center. Steel decking is complete and we have begun framing walls with metal trusses soon to follow. When complete, the building will house office and classrooms as well as a workshop on the first floor for repairs.
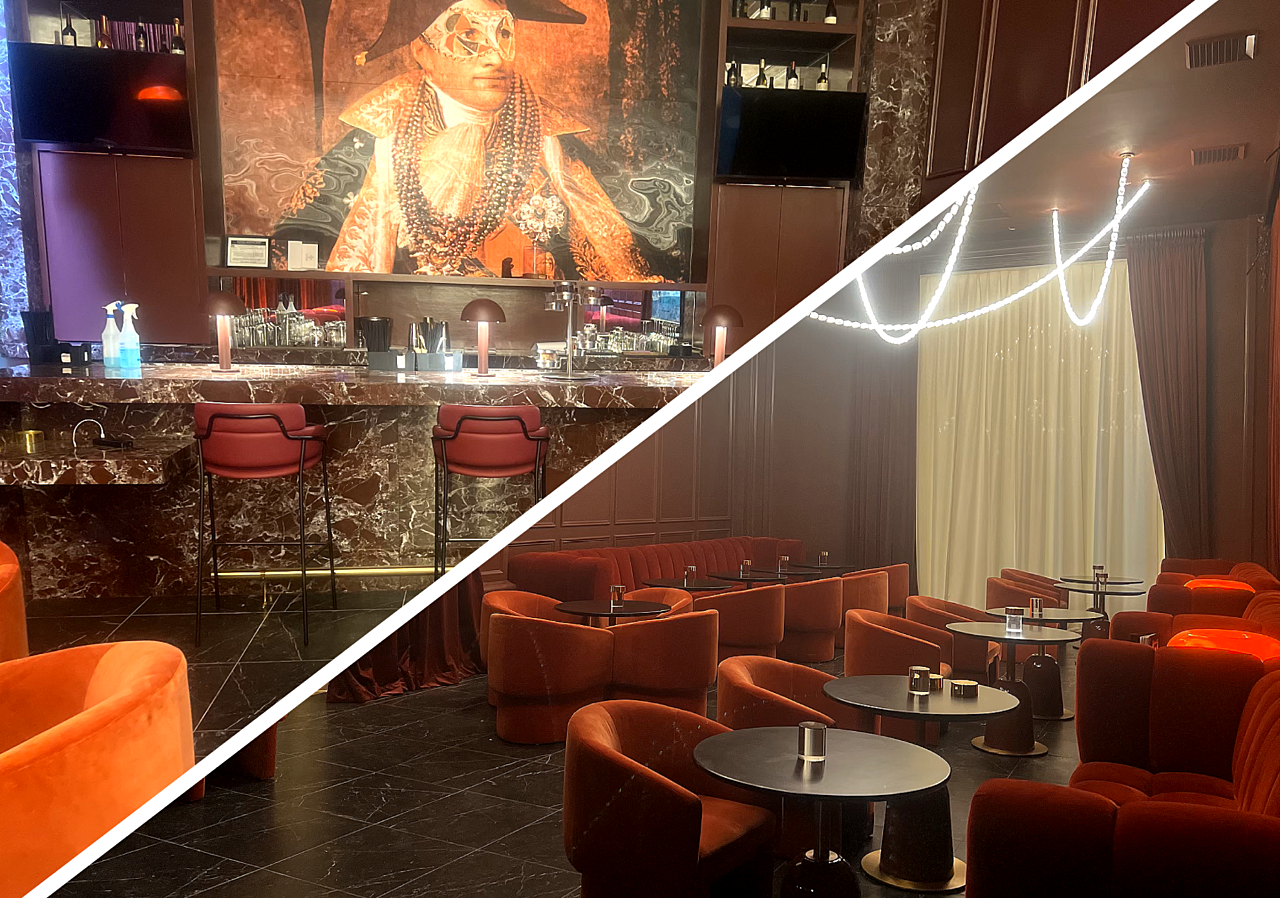
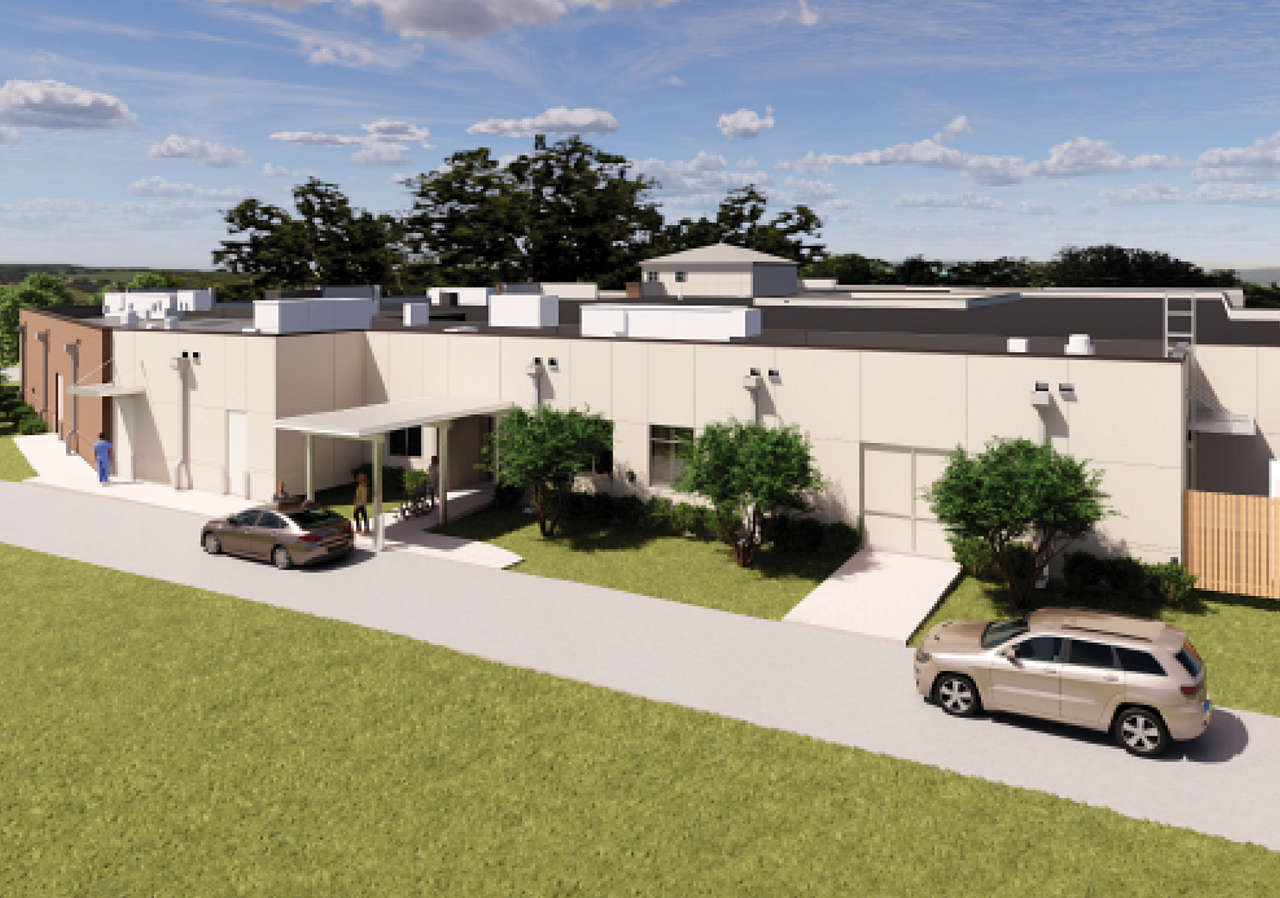
Le Pavilion Hotel
Our team is nearing completion of a comprehensive renovation across three floors of the Le Pavilion Hotel: the basement, and the first and second floors. The project scope covers 12 guest rooms and suites, eight meeting rooms, a bar and restaurant, and a fitness room, along with main lobby.
Bayou Bend Hospital
This two-phase project for Bayou Bend Hospital continues our success with the hospital. Phase one includes enhancements to the existing facility while phase two will focus on adding a new MRI suite and other infrastructure improvements. Both phases are scheduled for completion in 2025.
|
|
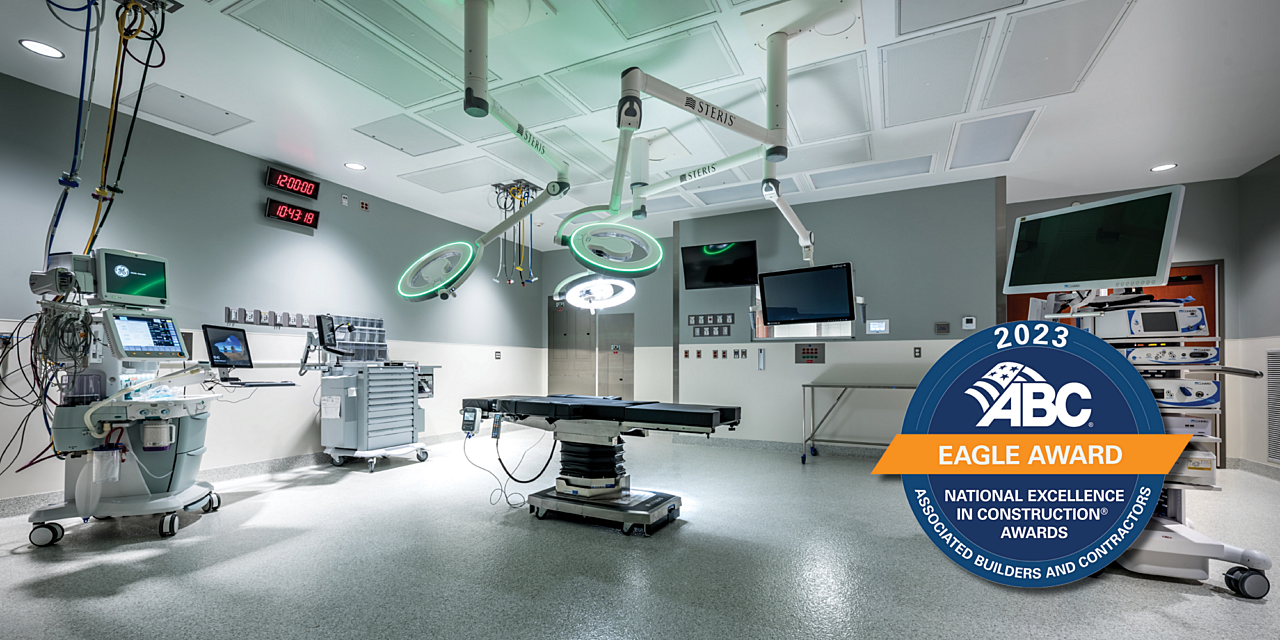
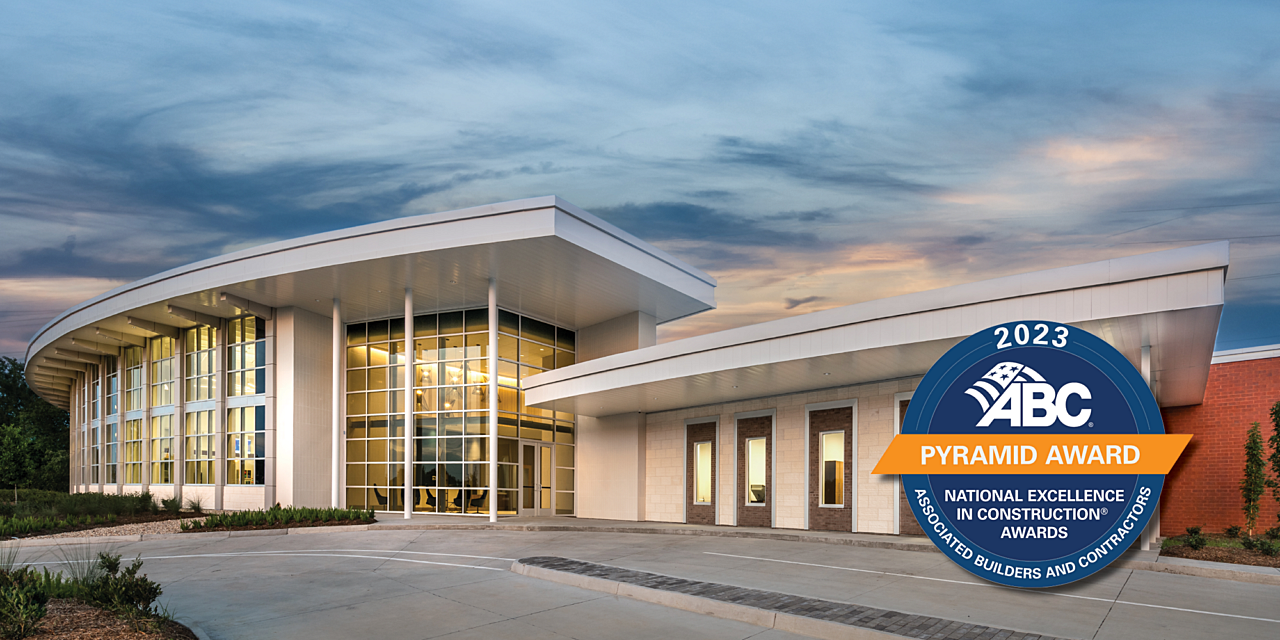
|
|
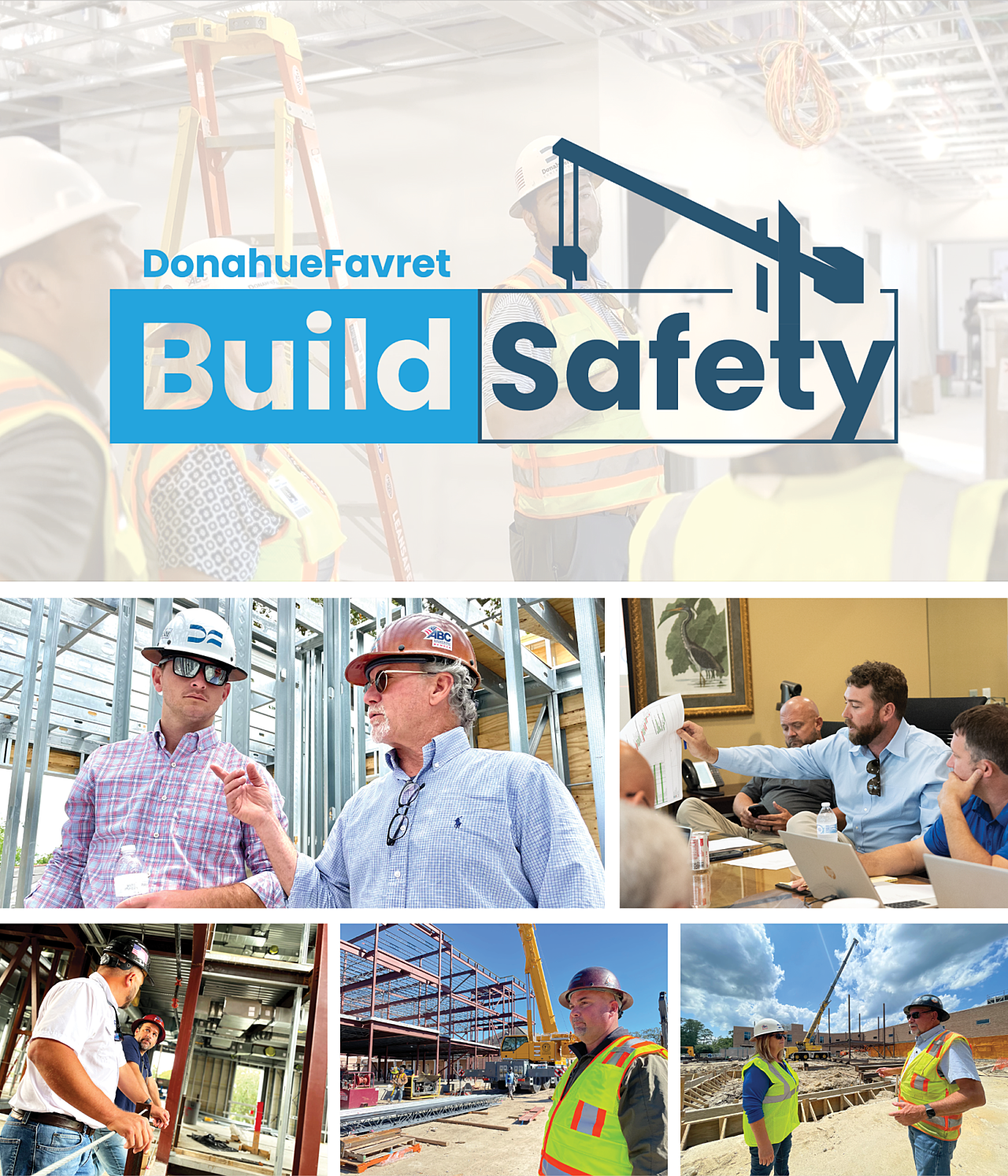
|
|
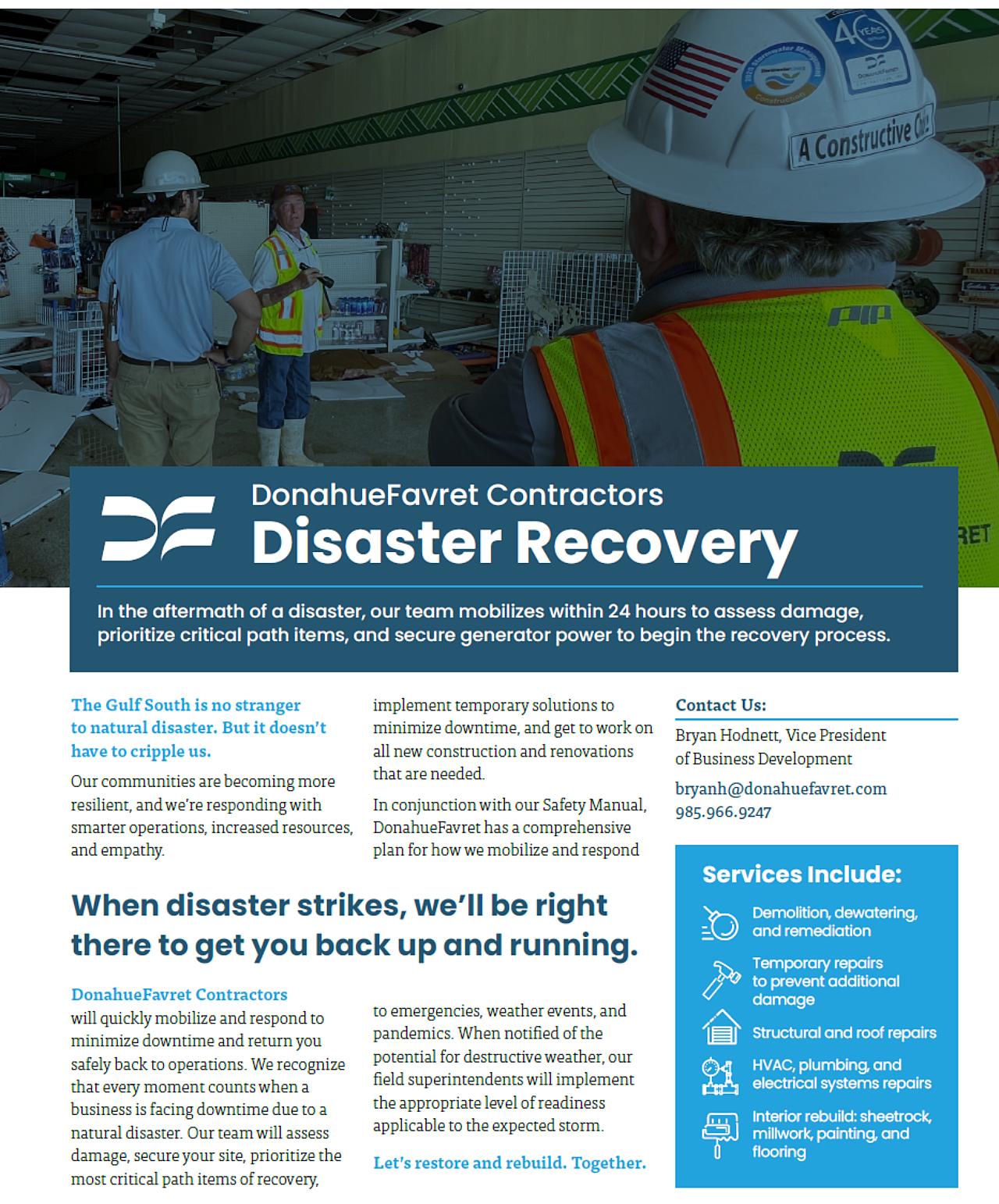
|
|
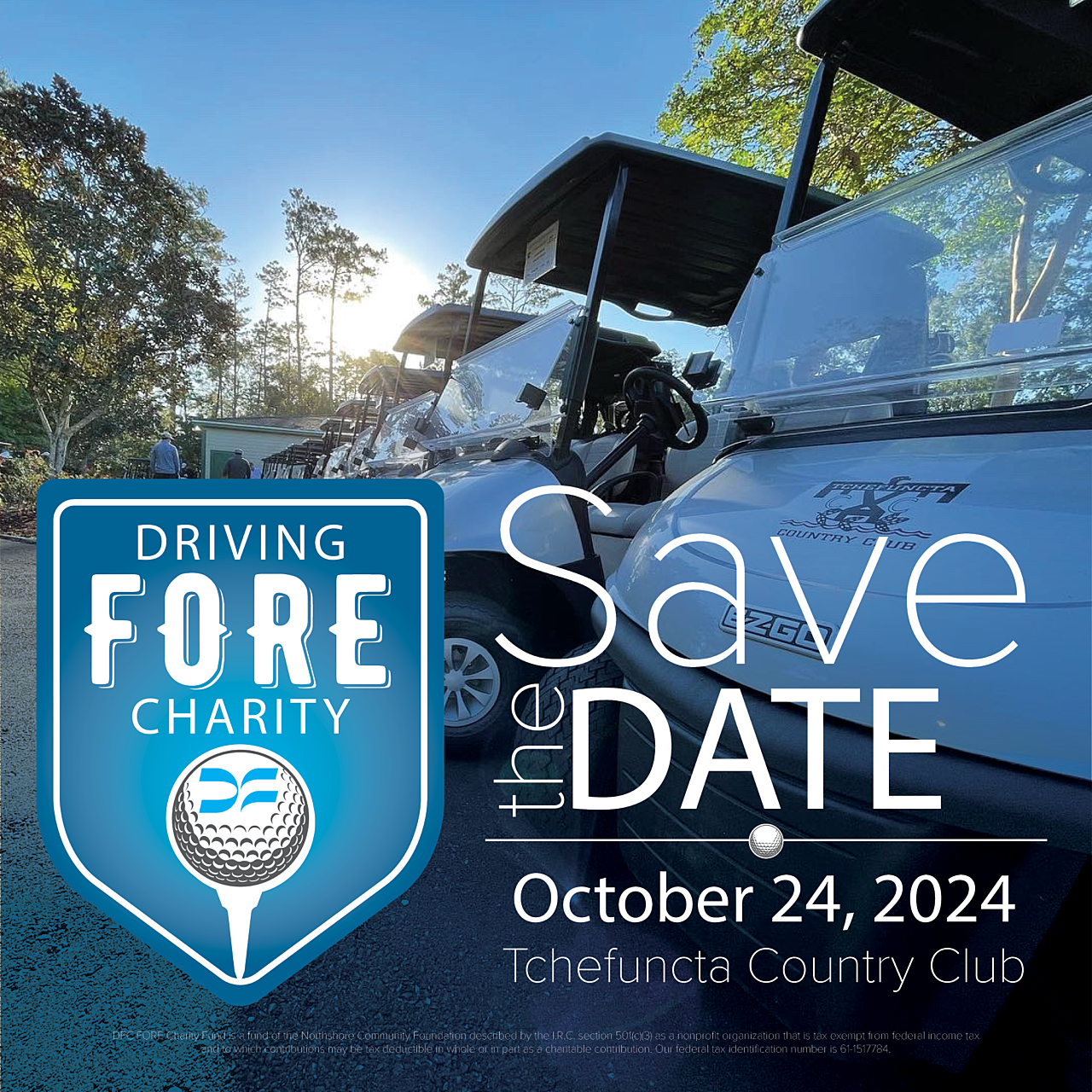