Strict regulatory standards and seamless integration present challenges to medical facility additions and renovations.
Building a new hospital addition and connecting it to an existing facility presents several challenges unique to healthcare construction, making these projects some of the most complex in the industry. The process involves tying together new and existing infrastructure, from complex mechanical and electrical systems to foundations and load-bearing structures. Adding to this complexity is the need to keep the hospital operational throughout the entire process. Every project phase must be carefully scheduled to avoid disruptions to essential services. Hospitals are sensitive environments, where even moderate noise or vibration can affect patient care, especially in intensive care units (ICUs), operating rooms, or diagnostic imaging areas.
Here, we explore several of the common hurdles facing these types of projects, and steps we often take to overcome them for successful project delivery.
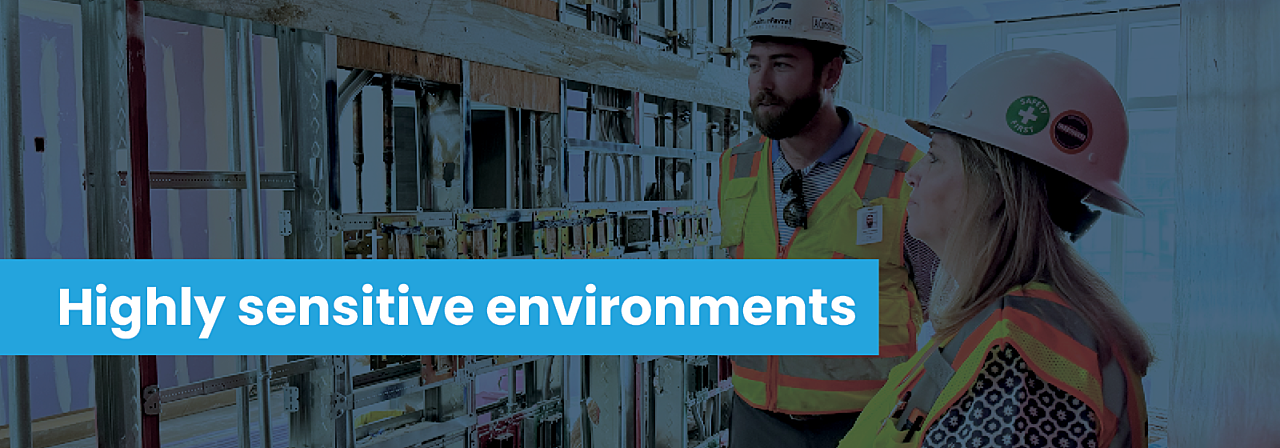
One of the most difficult aspects of hospital expansion projects is the integration of new MEP and HVAC systems into the existing facility. Hospitals are highly sensitive environments where uninterrupted power, air quality, and plumbing are critical for patient care. The challenge lies in ensuring that the new systems are compatible with the existing infrastructure while maintaining continuous operation of essential services. For example, HVAC systems in hospitals are designed to control air pressure, humidity, and filtration levels in different zones, including sterile and non-sterile areas. Any interruption in these systems could pose a significant risk to patient safety, particularly in areas like operating rooms or isolation wards.
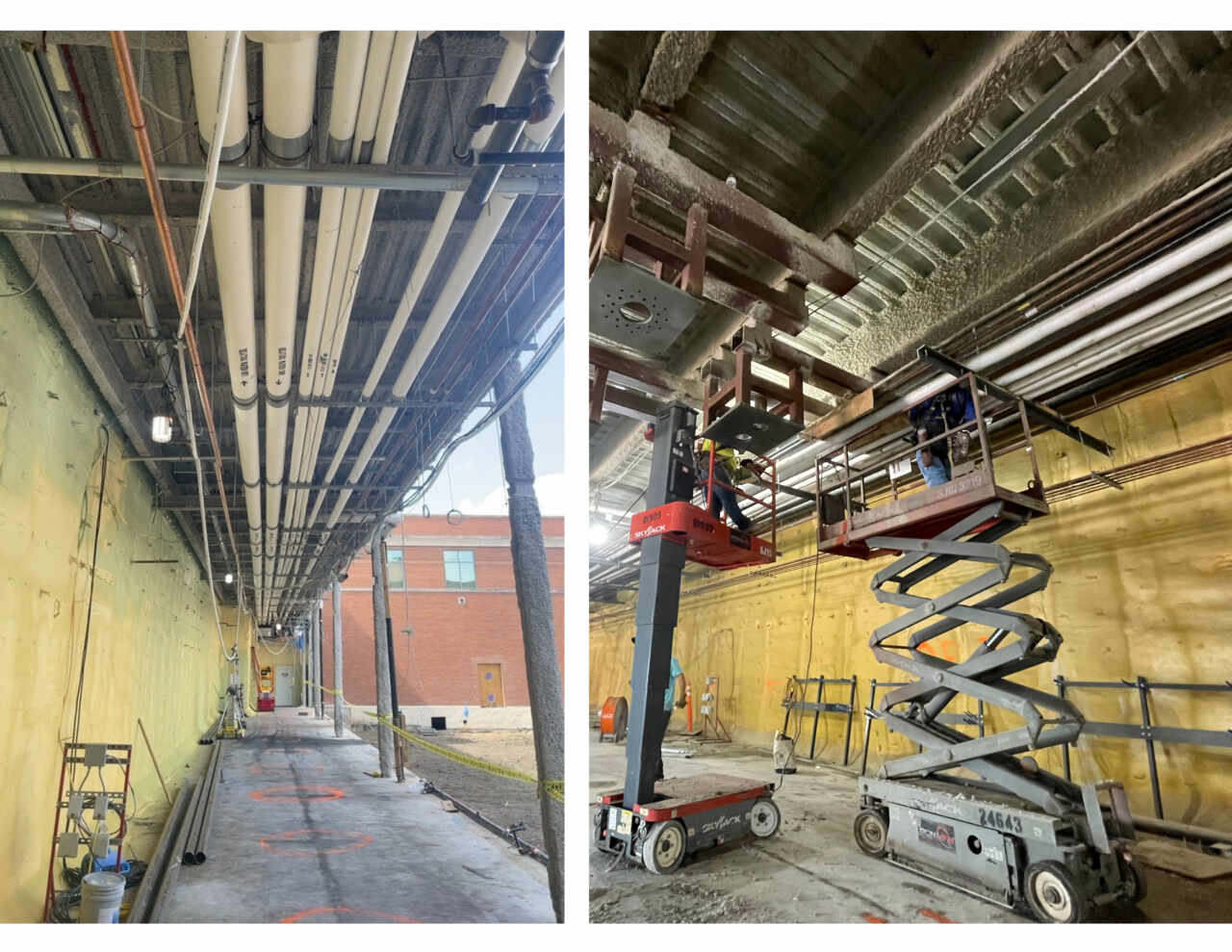
One of the most significant challenges when building the operating room expansion for Thibodaux Regional was working around the hospital's existing utilities.
Pipe racks were built to support utilities hung from the ceiling. The roof was then demolished, and new utilities were installed on the rack while the new structure was being erected in place.
Utility tie-ins and upgrades are particularly challenging because they may require temporary shutdowns. Hospitals rely on a constant supply of utilities, so contractors must schedule shutdowns for low-traffic times, often at night or on weekends, and even then, only after backup systems are verified and operational.

At Thibodaux Regional, our team and hospital staff worked closely to identify each of the different zones that could be impacted by any potential shutdown in power. This way, when the time came to run the final medical gas lines and tie-in to the existing facility, our team had the proper procedures in place to ensure no impacts were made to operations.
The highly sensitive nature of these environments coupled with the strict requirements in place for indoor air quality and pressure control demands higher standards for safe construction practices. ICRA – Infection Control Risk Assessment – guidelines ensure a safe and healthy environment is maintained throughout construction.
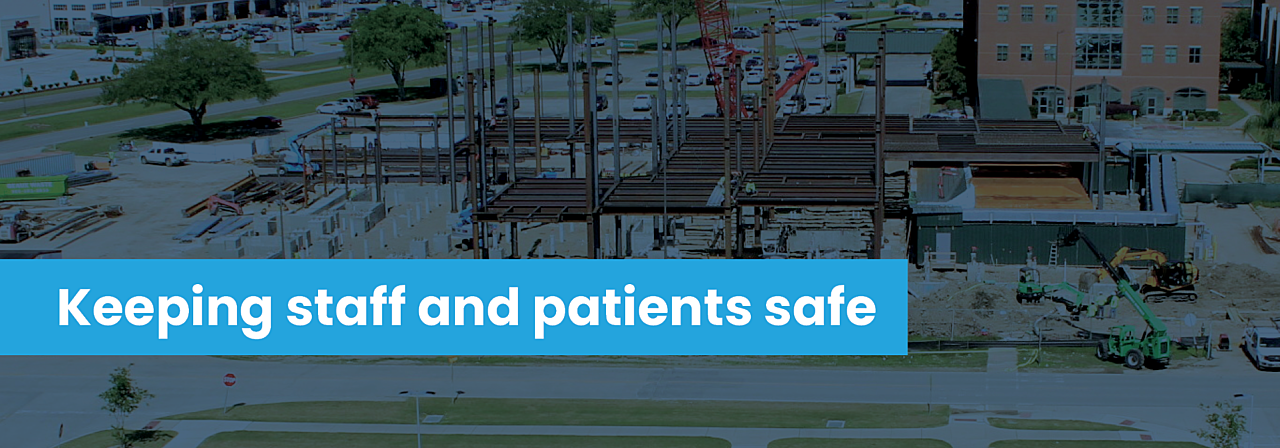
Infection Control Risk Assessment (ICRA) compliance in a hospital construction project introduces a level of complexity that’s often underestimated. The construction process generates dust, debris, and airborne particulates, all of which can be hazardous in a hospital setting. Patients, especially those in immune-compromised conditions, are at extreme risk if construction dust or pathogens infiltrate care areas.
One of the key challenges is creating effective containment zones that prevent dust and other particulates from spreading into patient care areas. This requires the installation of physical barriers - ICRA wall panels, often combined with complex negative air pressure systems - to ensure contaminated air from the construction zone does not leak into the existing facility. For instance, constructing a new intensive care unit (ICU) next to an existing one requires maintaining negative pressure in the construction area and strict adherence to HEPA filtration protocols to prevent the spread of any airborne pathogens.
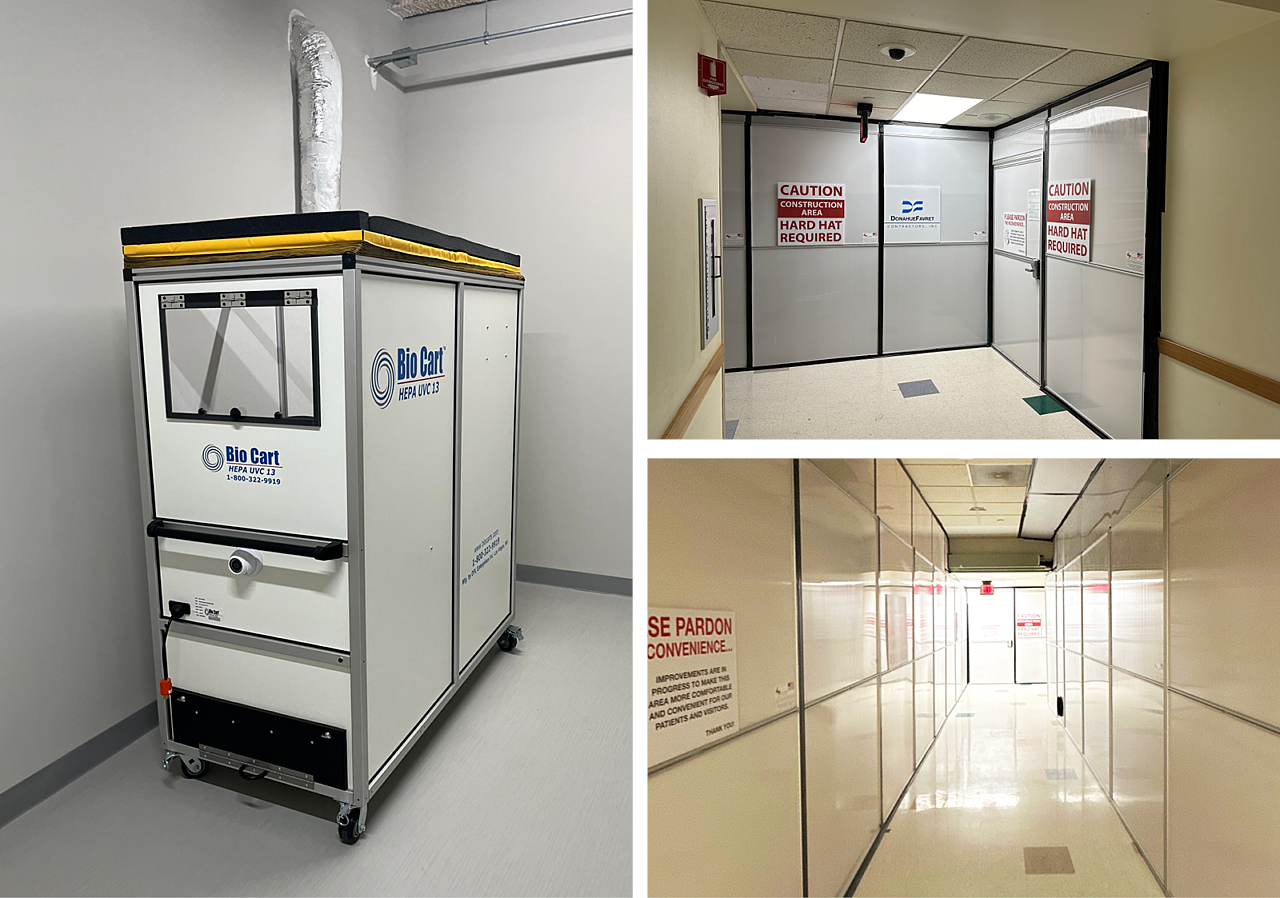
To protect patients and staff during the renovation of Tulane's 4th Floor Reily Pavilion, temporary ICRA wall panels were erected along the two main corridors of the floor. A negative air condition was established in a small anteroom that separated the construction work zone from the remaining hospital and fourth floor. Any material that exited the anteroom was covered and protected from cross contamination.
In many cases, these temporary walls or even enclosed pressurized corridors are created for logistical reasons to allow patients and staff to circulate safely around the jobsite. Here, phasing and sequencing of the work may be necessary to ensure no disruption to ongoing operations. DonahueFavret project managers and superintendents are trained and receive ongoing education under ICRA guidelines, each receiving ICRA certification that is maintained on an annual basis.
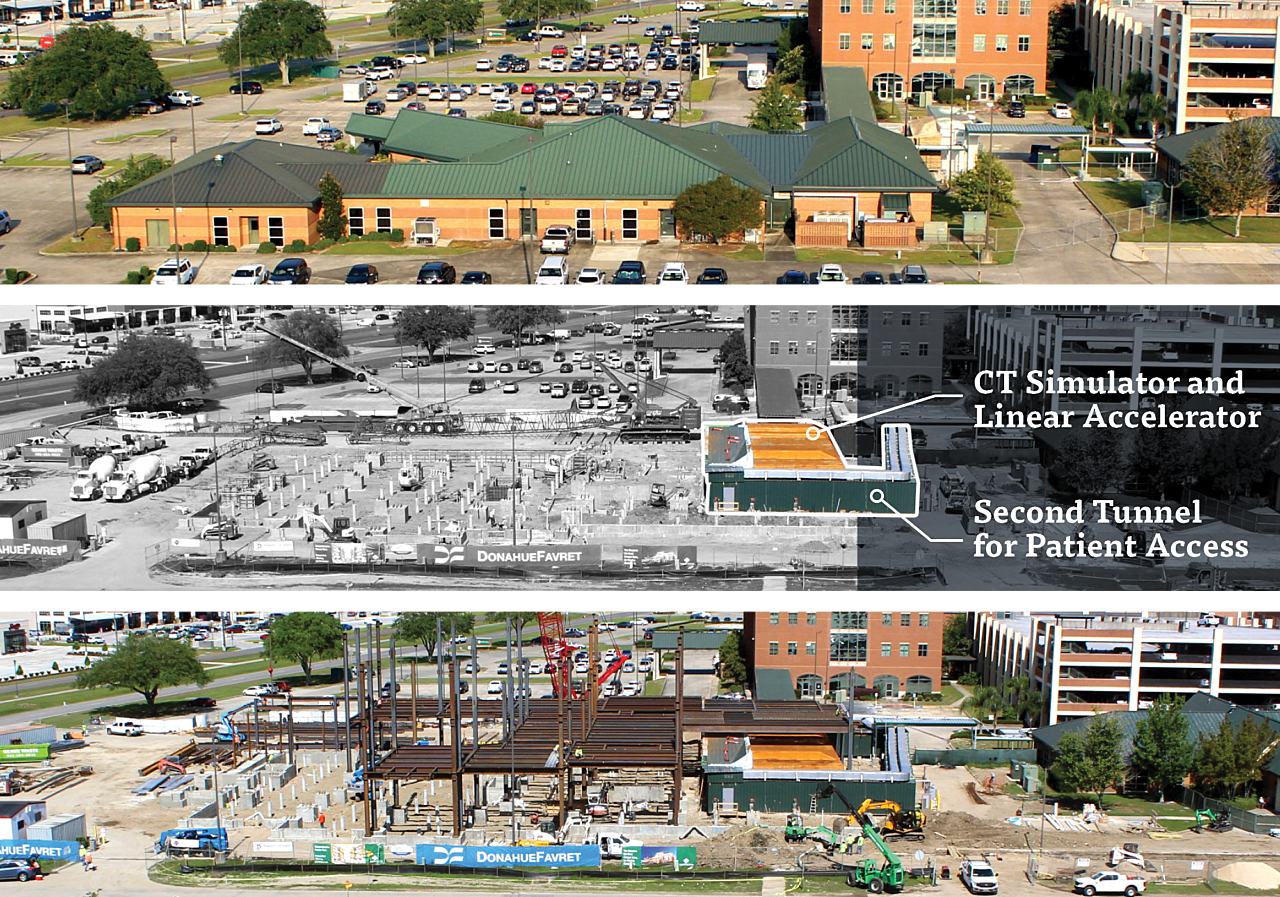
Early construction of the Thibodaux Regional Cancer Institute involved several phases of pile driving, all while needing to keep access open to the existing CT Simulator to remain on site. Three separate prefabricated and sealed tunnels were built to allow patients ongoing safe access to vital medical equipment while construction progressed around the existing structure.
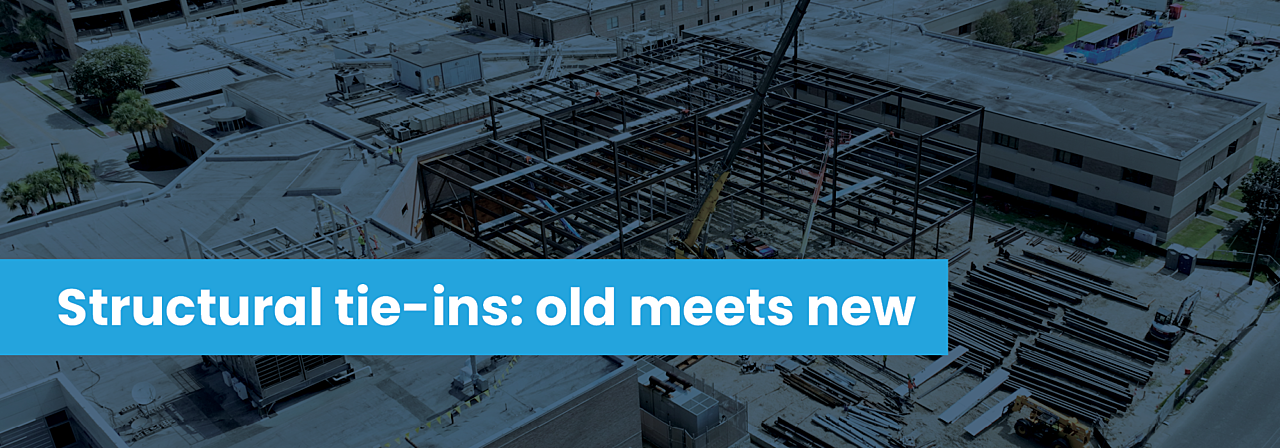
Physically connecting the new structure to the existing facility presents a major challenge. Hospitals are often built over several decades, which means that the existing structure may be a patchwork of different construction materials, techniques, and sometimes design codes.
For example, the existing facility may have settled over time, complicating the process of tying in a new addition. The challenge lies in ensuring that the two structures remain stable and do not create stress at the connection points. If not properly accounted for, differential settling can lead to cracks in the structure, water leakage, or even safety hazards. Hospitals often have strict requirements for clearances for things like patient beds, medical carts, and gurneys, for example. Ensuring seamless transitions between floors is essential. In some cases, differing slab heights or structural systems in the older building may require ramps or intermediate landings, which need to be engineered for accessibility without compromising the flow of patient traffic.
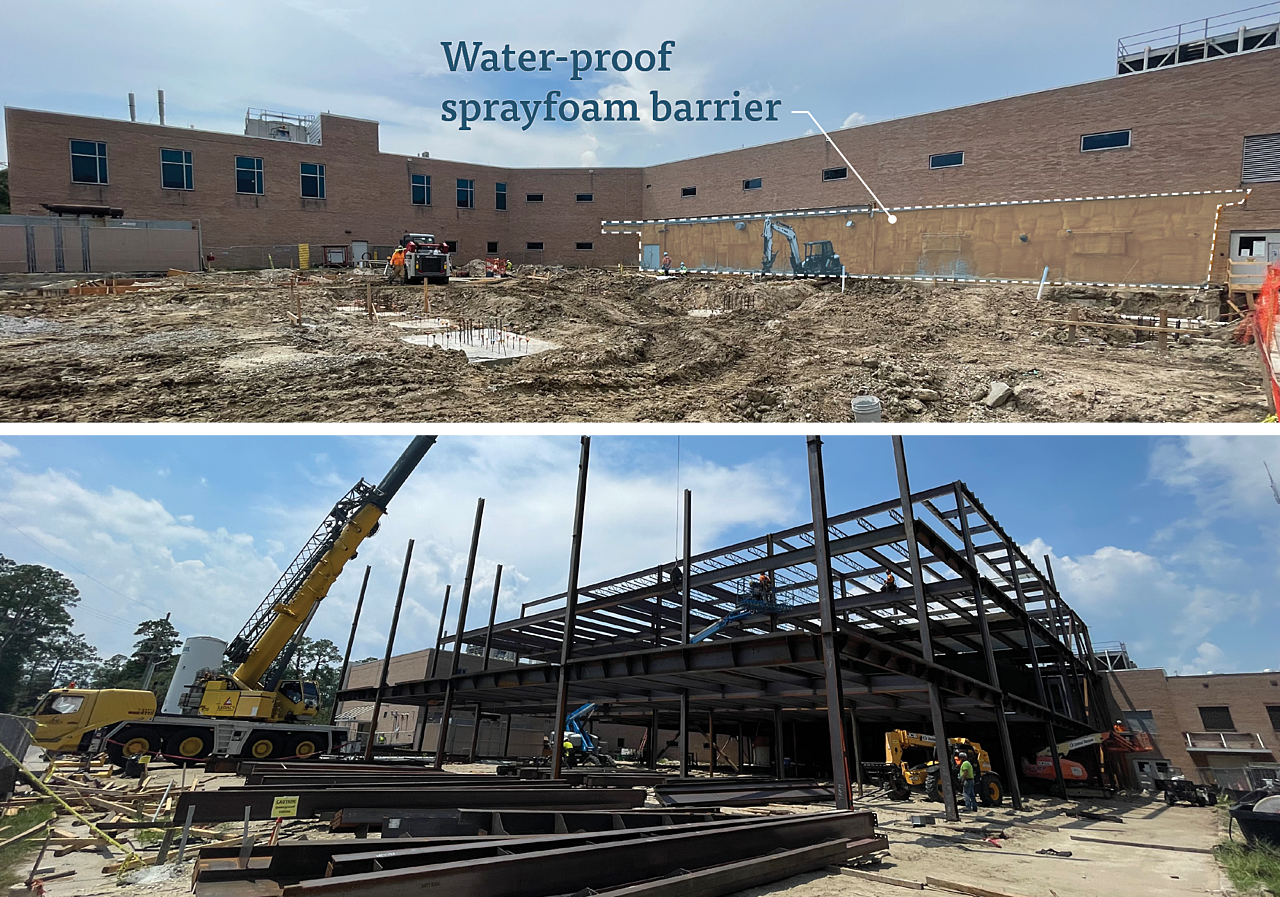
The recently completed addition for Slidell Memorial Hospital tied the new facility into the existing hospital. Demolition involved creating an opening on the existing facility where the new structure would tie-in. To protect the existing space from the open-air environment, a unique closed cell spray foam insulated barrier was applied to the opening, waterproofing the space until the new addition's structure was constructed and dried in.
The process of joining a new addition to an existing facility includes demolishing the existing exterior façade, exposing the current facility to the open-air environment. To mitigate this, waterproofing and sealing the existing adjacent space is crucial. In some cases, closed cell spray foam insulation is used in this case to provide a waterproof barrier between the existing occupied space and the new addition until it can be dried in.
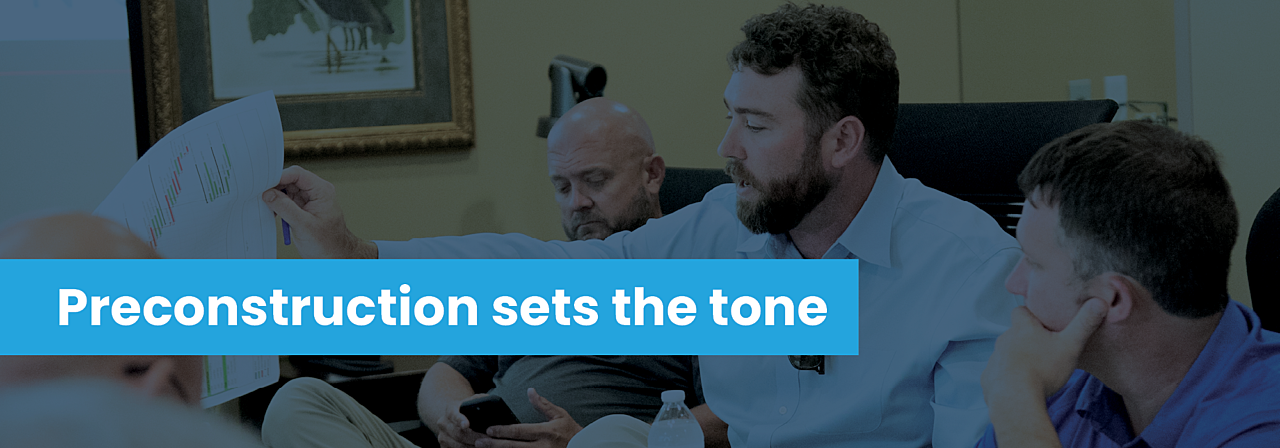
Each of these challenges, both anticipated and unforeseen, are addressed, planned for, and overcome only after a comprehensive preconstruction process. For example, identifying early in design where critical tie-in points are located will ensure that all new infrastructure (mechanical, electrical, plumbing, and data) integrate seamlessly with current systems. Proper sizing of new equipment is essential and can even setup the addition for successful expansion in the future. Without this early proactive investigation, schedule and/or budget will be impacted later in construction. Phasing and sequencing, critical for not only maintaining the project’s schedule, but also to ensure patient and staff safety, is identified during preconstruction. Additionally, identifying the right team of trade partners during this phase with relevant experience ensures that complex tasks are executed with precision, reducing the risk of delays.
During preconstruction, our operations team – those who will be managing the project during construction – are involved in these critical design phases to ensure a seamless transition from design and planning to construction.
The complexities of hospital expansion projects, especially those that tie into existing facilities, are numerous and multi-layered.
From the technical challenges of merging MEP systems to the structural difficulties of physically connecting buildings, and from maintaining compliance with strict infection control standards to ensuring the hospital remains fully operational throughout, each aspect requires careful planning and precise execution.
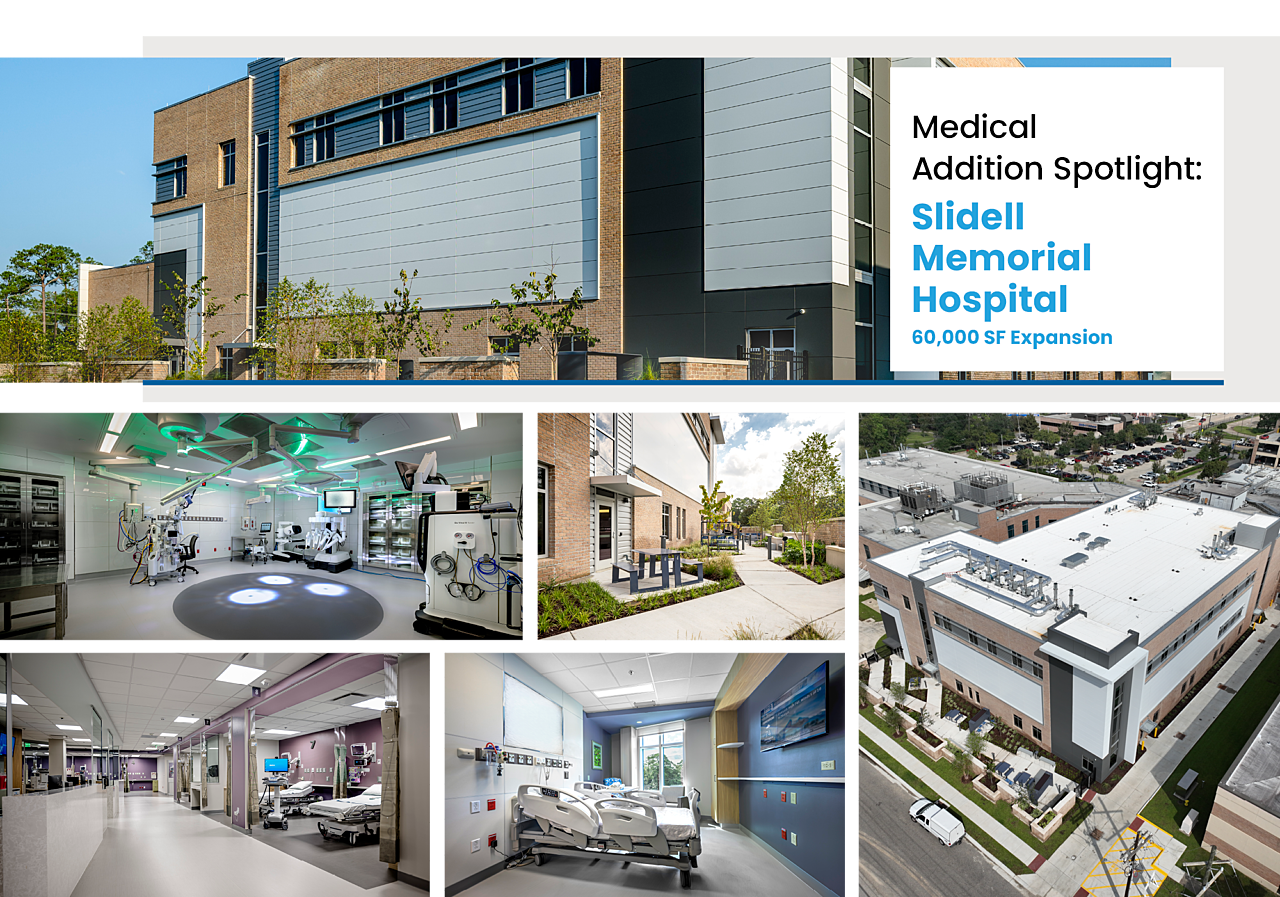
Slidell Memorial Hospital's Addition Sets New Precedent in Healthcare Construction.
Recently our team completed a new 60,000-square-foot 3-story addition of Slidell Memorial Hospital, navigating many of the same challenges mentioned above. This project expanded the main campus of the hospital with a new building that houses a new set of operating suites, an additional intensive care unit, and additional inpatient care with private rooms. The project also includes the demolition of existing structures and renovation of the current operating rooms, built in the 1970s, to create a surgical experience that is completely private for patients, without the need to be transported along public corridors to and from surgery.
Stay tuned soon for a full case study on this transformative project.
Noteworthy Projects Under Construction
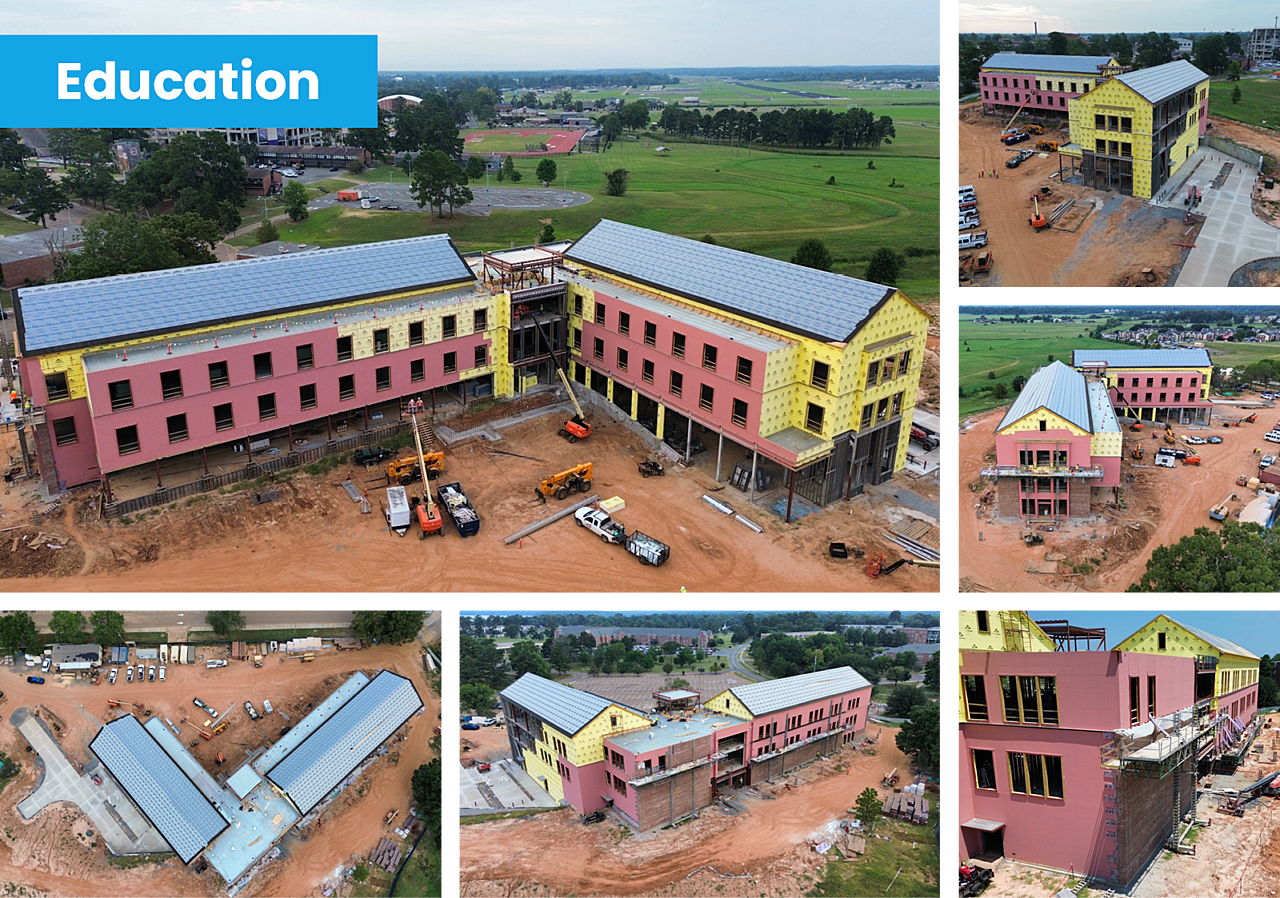
After a successful beam signing event in May, our team continues to make great progress on this new 72,000-square-foot multi-story classroom for Northwestern State University When complete, the building will consist of multi-purpose classrooms, teaching labs, simulation clinics, administrative offices, student collaboration spaces, and support areas.
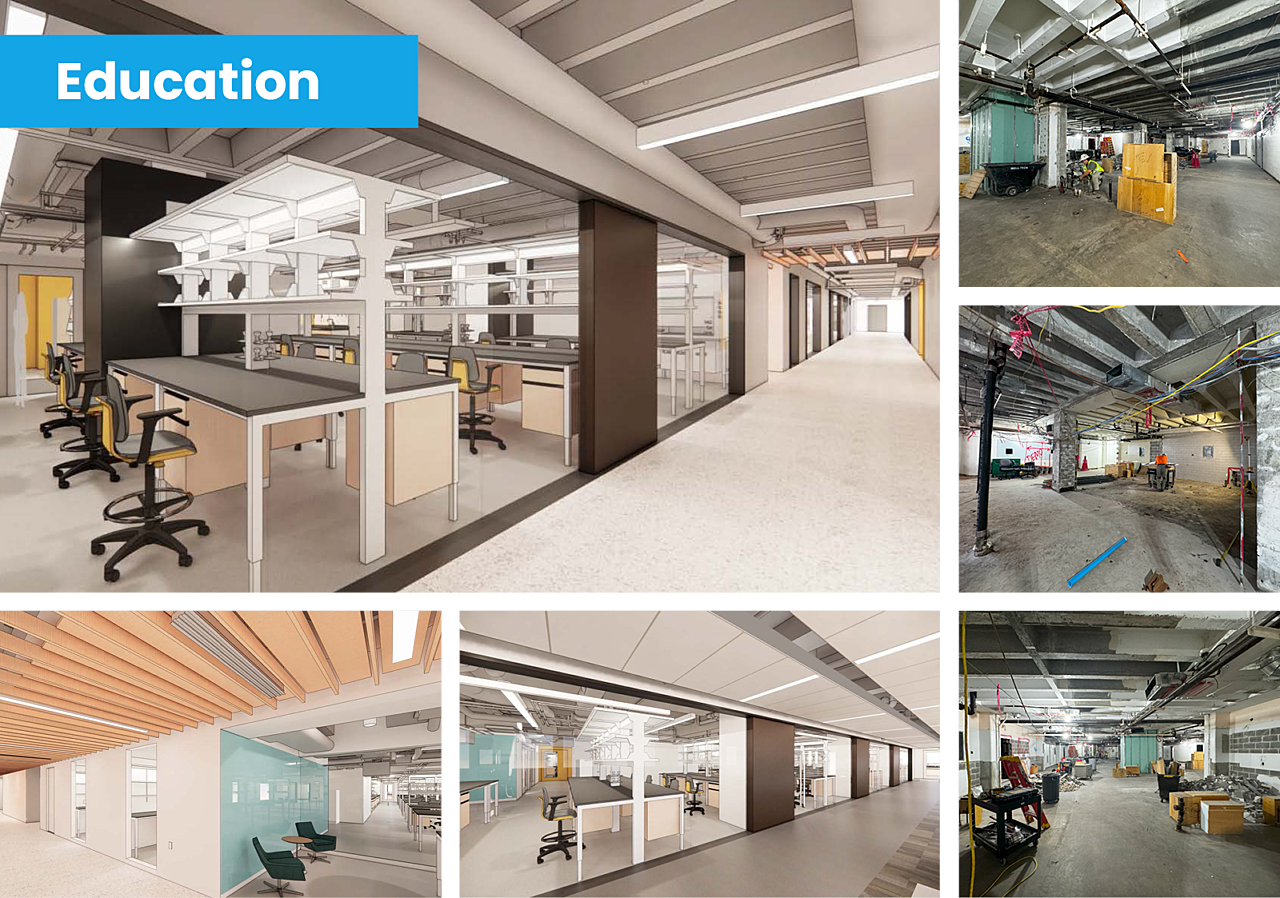
DonahueFavret has begun the renovation of the 7th Floor of Tulane University’s Hutchinson Building. Interior renovations will follow full demolition of the existing space. Renovations will include new critical laboratory facilities, write-up area, and office space across 48,000 square feet. MEP systems will tie into the facility’s existing infrastructure. The project is scheduled for 14 months including demolition and is targeting LEED Silver.
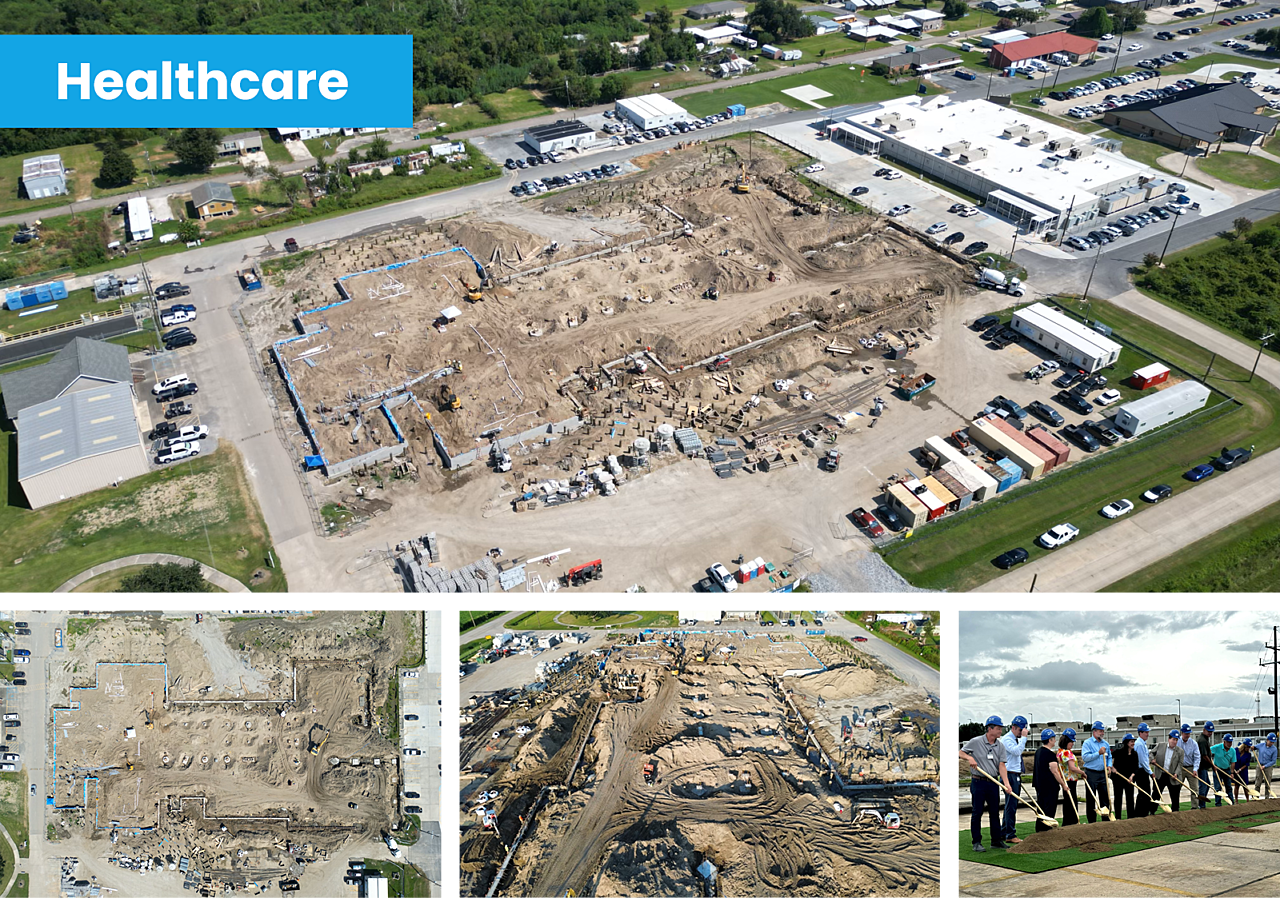
The new ground-up 80,000 SF hospital for Lady of the Sea is now underway. More than 1,700 70-foot timber piles have been driven and the pouring of concrete slabs is now underway. The team recently completed two of five main slab pours totaling approximately 30,000 SF and 1,200 cubic yards. There will be an additional four auxiliary pours to follow.
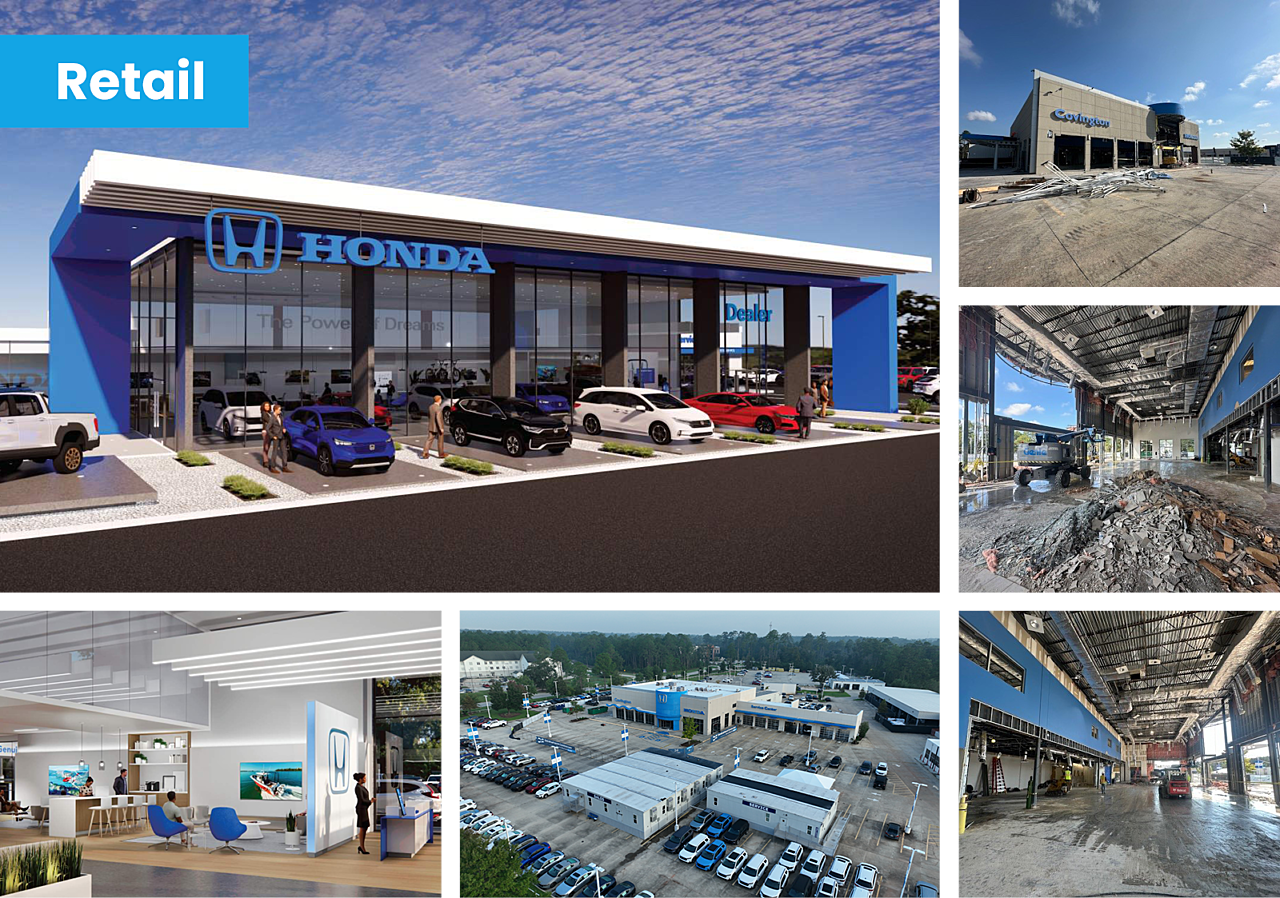
Our team recently began a 6-month renovation process for Honda of Covington with demolition well underway. When complete, the project will deliver 16,300 square feet of renovated space including new storefront and showroom area.
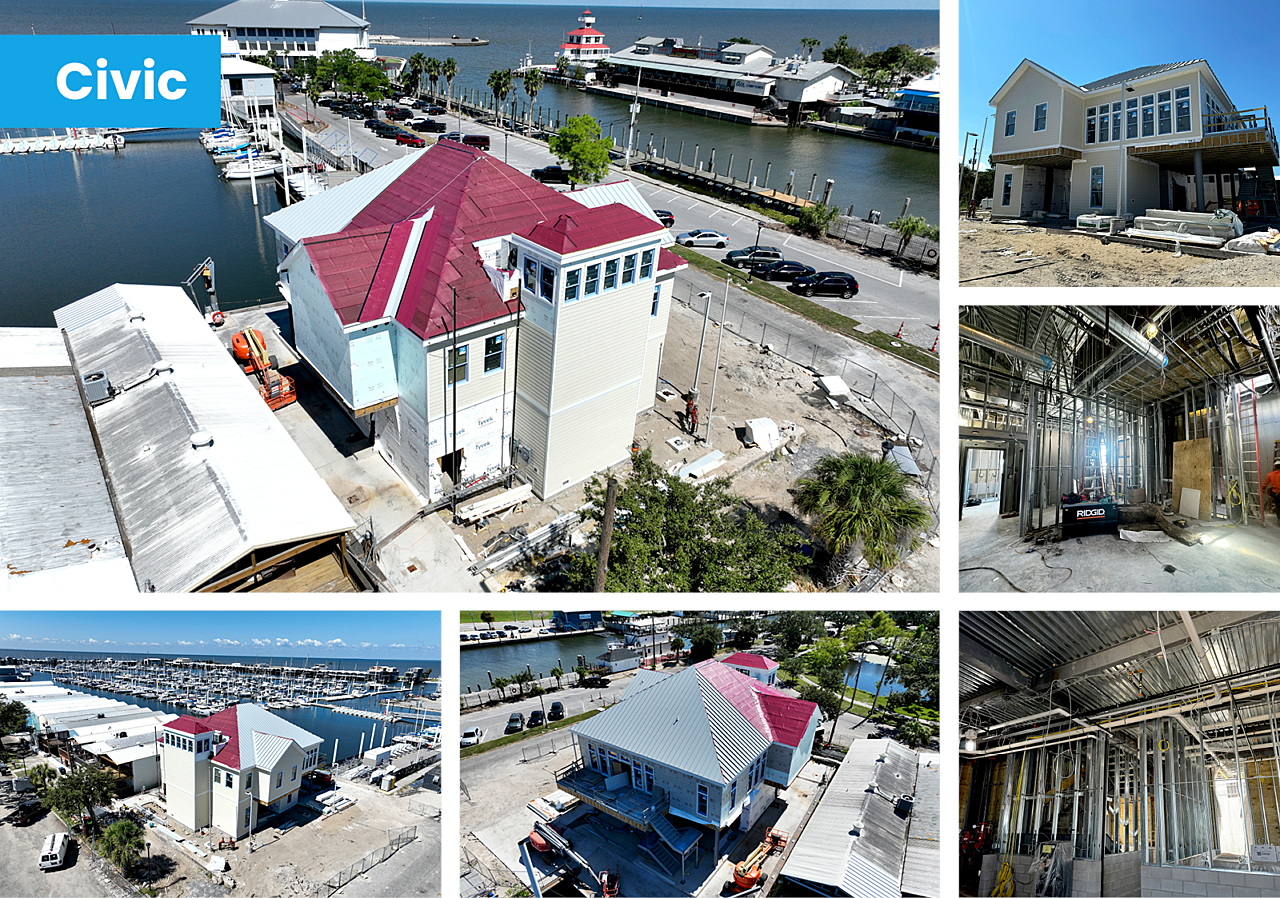
Progress continues on the New Orleans Community Sailing Center. We are currently in the process of installing drywall, exterior siding, and finished roof panels. Then next phase will include painting and flooring. The project is on track for a fourth quarter grand opening.
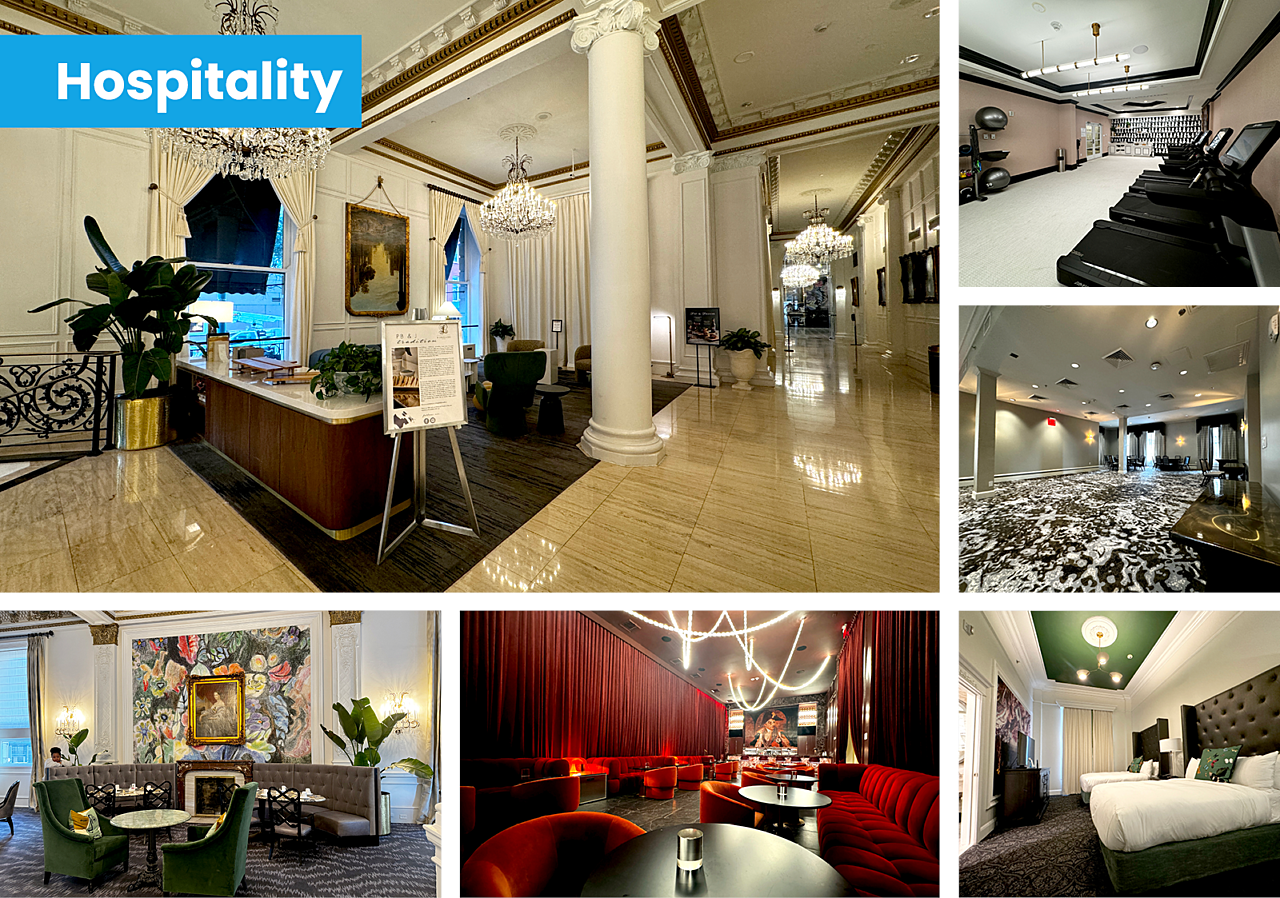
Our team is nearing completion of a comprehensive renovation across three floors of the Le Pavilion Hotel: the basement, and the first and second floors. The project scope covers 12 guest rooms and suites, eight meeting rooms, a bar and restaurant, and a fitness room, along with main lobby.